Produkt-News >>>
GÜNTHER Heisskanaltechnik lädt auf der Swiss Plastics Expo 2023 zur Premiere in der Schweiz ein: Erleben Sie die Präzision der smarten Temperatur-Regler blueMaster compact und blueMaster pro. Die neue Regler-Generation des Technologieführers aus Frankenberg/Deutschlamd punktet mit optimalen Regelungseigenschaften, umfassender Konnektivität und einer komfortablen Bedienung. Überzeugen Sie sich von der maximalen Energieeffizienz der BlueFlow® Heißkanaldüse und informieren Sie sich über schnelle und kostengünstige Lösungen zur Produktivitätssteigerung und Energieeffizienz.
blueMaster: Die neue Generation von smarten Reglern Eine leistungsfähige und präzise Regeltechnik maximiert die Produktivität und die Produktionsqualität. Mit der neuen smarten Technologie blueMaster, die die Varianten blueMaster compact (3 – 6 Regelkreise) und blueMaster pro (6 – 24 Regelkreise) umfasst, präsentiert GÜNTHER neue Wege in Richtung Industrie 4.0. Die Geräte verfügen über optimale Regelungseigenschaften, umfassende Konnektivität, kompakte Abmessungen sowie eine smarte Bedienung.
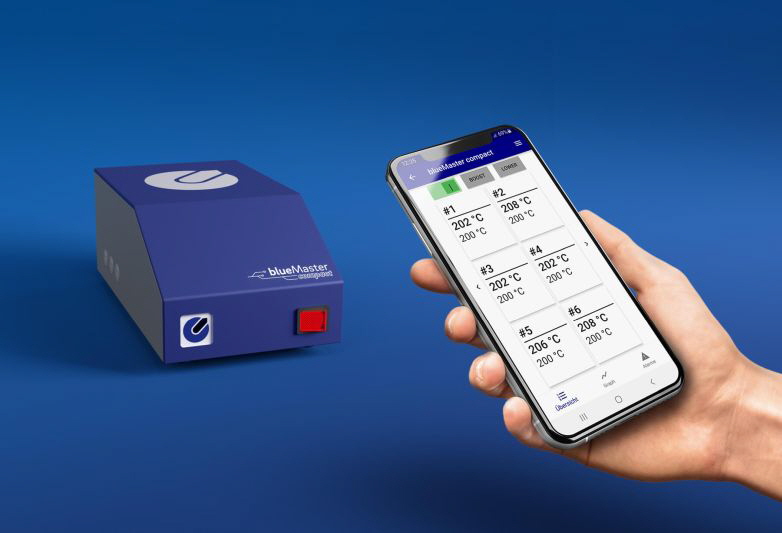
Maximale Energieeffizienz mit der BlueFlow® Heißkanaldüse Mit fast 40-jährigem Know-how entwickelt GÜNTHER zukunftsweisende Technologien für mehr Energieeffizienz und Ressourcenschonung. Mit der BlueFlow®-Heißkanaldüse können im Vergleich zu konventionellen Heizungen – je nach Systemauslegung – bis zu 50% Energie eingespart werden. Möglich macht dies die innovative Dickschichtheizung und der patentierte, zweigeteilte Schaft.
â–ºWeitere Informationen finden Sie hier.
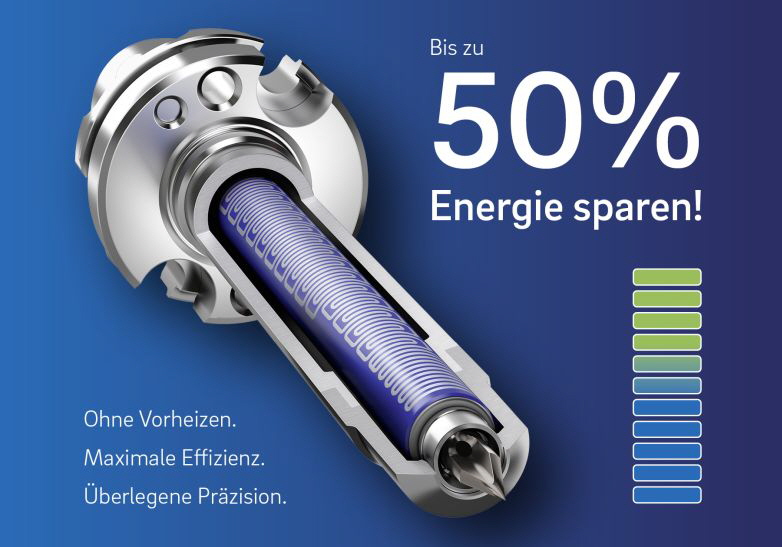
Produkt-News
Präzise Regelung verbessert die Qualität
Eine präzise und komfortable Prozesskontrolle ist beim Spritzgussprozess zur Sicherstellung der Produktqualität unumgänglich. GÜNTHER Heisskanaltechnik sorgt mit seiner neuentwickelten Regel- technik blueMaster pro für optimale Regelungseigenschaften und eine umfassende Konnektivität für 6 bis 24 Regelkreise.
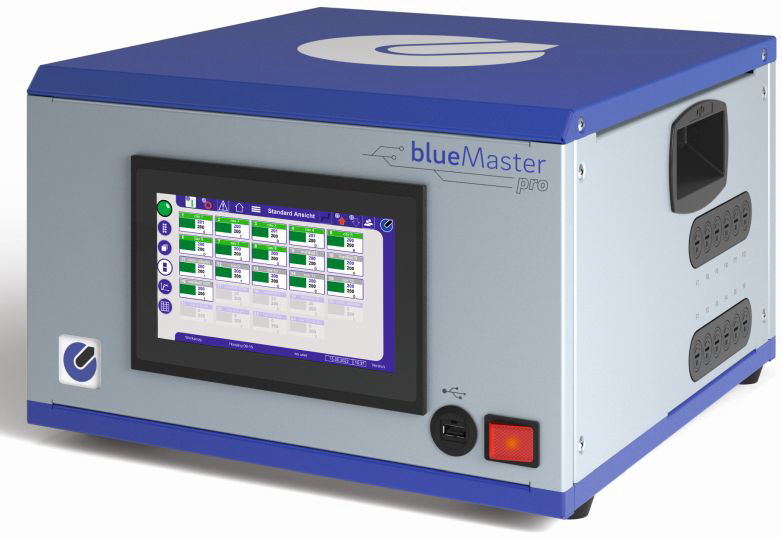 Die neue Regler-Baureihe blueMaster pro von GÜNTHER bietet eine volle Bedienbarkeit über eingebautes Display und per Browser.
Im Spritzgießprozess muss der Heißkanal sowohl beim Aufheizen als auch beim Halten der Solltemperatur exakt und gleichmäßig beheizt werden, somit steht die Qualität des Spritzgussteils in direktem Zusammenhang mit der Genauigkeit der Temperaturregelung. Deshalb ist eine leistungsfähige und präzise Regeltechnik mit optimalen Regelungseigenschaften unabdingbar. Auf der Fachmesse K 2022 hat der Technologieführer im Bereich Heißkanal- und Kaltkanaltechnik eine neue Produktreihe für die sichere Regelung komplexer Heißkanalsysteme vorgestellt. Deren neue Bedienoberfläche ermöglicht eine intuitive Bedienung sowohl direkt am Gerät als auch per Browser.
Das Regelgerät blueMaster pro wird in vier Varianten für 6 bis 24 Regelkreise angeboten. Handelt es sich auf den ersten Blick um klassische Auftisch-Regler mit eingebautem Display, liegt die Besonderheit darin, dass sie auch per Browser bedienbar sind. So kann der Anwender per Tablet auf mehrere Geräte zugreifen oder aus dem Leitstand schnell den Betriebszustand seiner Geräte erfassen und nötigenfalls eingreifen. Beim Einrichten neuer Werkzeuge unterstützt eine Assistenzfunktion. Höherfachige Werkzeuge und Mehrkomponenten-Systeme lassen sich über die integrierte Gruppenverwaltung komfortabel bedienen. Ein Schlüssel für die Vernetzung der Temperaturregelung ist die Standardisierung der Datenschnittstellen. Die neuen Heißkanalregler blueMaster pro unterstützen die Euromap 82.2 in vollem Umfang. Diese Norm beschreibt die Schnittstelle zwischen Spritzgießmaschinen und Heißkanalreglern für den Datenaustausch. Sie basiert auf der OPC Unified Architecture Schnittstelle (OPC UA), einem Kommunikationsstandard für den sicheren und zuverlässigen Datenaustausch im Bereich der industriellen Automatisierung.
Neue Möglichkeiten in Richtung Industrie 4.0 Der blueMaster pro verfügt über ein schmuckes wie robustes Metallgehäuse an dem alle Lastsicherungen komfortabel von außen zugänglich sind. Die Last- und Thermoanschlüsse können nach Kundenwunsch ausgeführt werden. Standardmäßig ist ein 7-Zoll-Display für die grafische Benutzeroberfläche integriert. Dabei kann der Benutzer jederzeit auch z.B. per Tablet auf das Gerät zugreifen. Für die Bedienung des Gerätes kann der Benutzer aus fünf verschiedenen Ansichten die wählen, die ihm für seine Anwendung am sinnvollsten erscheint. So ist neben einer grafischen Anzeige der Temperaturen auch eine übersichtliche Tabellenansicht und für komplexere Systeme die Gruppenansicht verfügbar.
Neben dem schon erwähnten Einrichte-Assistenten ist auch eine Heißkanal-Diagnosefunktion integriert, um etwaige Fehler schnell aufspüren und beheben zu können. Der blueMaster verfügt über alle Funktionen, die der Anwender für eine sichere Regelung komplexer Heißkanalsysteme benötigt. Die intuitive Bedienung sowohl auf dem Display, dem Tablet oder am Leitstand ermöglicht es, sich ohne Einarbeitungszeit schnell zurecht zu finden. Die Hilfefunktion ist kontextabhängig, so dass der Benutzer direkt und im Klartext die Information erhält, die er gerade benötigt.
Christoph Münch, Projektleiter Regeltechnik bei GÜNTHER Heisskanaltechnik, „Mit den neuen Premium-Reglern blueMaster pro eröffnen wir den Nutzern neue Möglichkeiten in Richtung Industrie 4.0 und gehen weit über den herkömmlichen „Smart Control Service“ hinaus. So lassen sich z.B. alle Messdaten schnell und sicher in eine Cloud hochladen und für die Dokumentation oder eine detailliertere Auswertung nutzen.“ Christoph Münch fasst zusammen. „Werden andere Regler immer komplexer und komplizierter in ihrer Bedienung, gehen wir den anderen Weg und bieten zukunftssichere, einfachere Lösungen, die die Anwender unterstützen und ihre Arbeit erleichtern.“
Die „Easy to use“-App
Eine intuitive Bedienung von Regelgeräten für den Heißkanal kann die Ressourceneffizienz im Spritzgussbetrieb erhöhen. Auch deshalb hat GÜNTHER für seine neue smarte Regeltechnik eine App entwickelt, die auch für Anwender ohne Spritzgießausbildung leicht nutzbar ist.
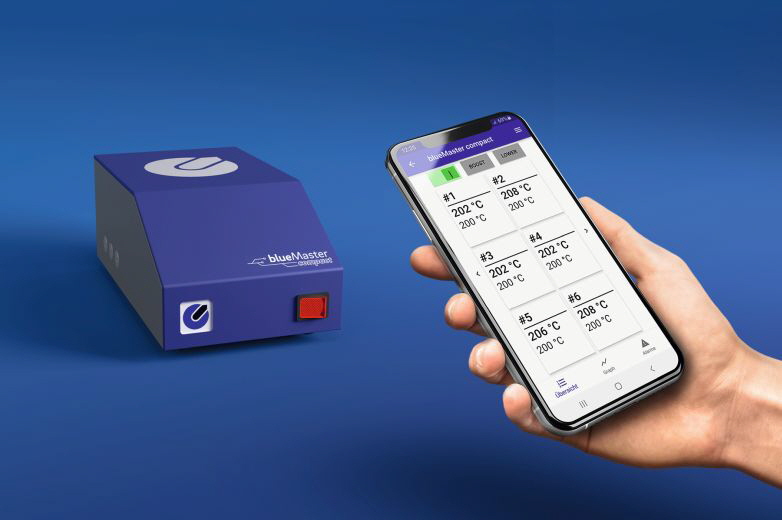 GÜNTHER mit seiner neuen blueMaster-Reglerreihe auf der K.
Auf der K, Messe 2022 hat der Technologieführer im Bereich Heißkanal- und Kaltkanaltechnik, GÜNTHER Heisskanaltechnik, eine neue Regeltechnik vorgestellt, die optimale Regelungseigenschaften und eine umfassende Konnektivität aufweist. Die dazu passende neue App ermöglicht zudem eine intuitive Bedienung.
Alle wichtigen Parameter auf einen Blick Die App wurde entwickelt, um die Bedienung der Regelgeräte weniger komplex zu machen, so dass sie auch Werker ohne Spritzgießausbildung verwenden können. Das anwenderorientierte Intro mit nützlichen Erklärungen gestaltet die Bedienung so einfach, dass eine Anleitung praktisch obsolet ist. „Wir haben die modernen Interfaces schon heute in der Tasche oder am Arm. Smartphones oder Tablets können wir spielend bedienen. Warum also nicht einfach den Regler mit dem Smartphone steuern“, sagt Christoph Münch, Projektleiter Regeltechnik bei GÜNTHER Heisskanaltechnik. „Wir haben uns als Hersteller gefragt: Was sind die wichtigsten Funktionalitäten unseres Produktes? Welche Funktionen sind so elementar, dass der Nutzer sie auf Anhieb ausführen können muss? Denn diese Funktionen sollten mindestens auf die Erfahrungen und Erwartungen der Nutzer ausgerichtet sein.“ Herausgekommen ist eine zeitgemäße Menüführung mit grafischen Temperaturanzeigen, die für den Nutzer leichter zu interpretieren sind. „Zudem hat dieser alle wichtigen Parameter auf einen Blick parat,“ ergänzt Christoph Münch. „Alle Messdaten lassen sich ferner schnell und sicher in eine Cloud hochladen und für die Dokumentation oder eine detailliertere Auswertung nutzen.“ Die App lässt sich auf alle gängigen Smartphones oder Tablets aufspielen und ermöglicht so eine Steuerung der Regelgeräte unabhängig vom Aufstellort. Die Kommunikation erfolgt über Bluetooth, sodass auch mehrere Regler bedient werden können. Das im Regler integrierte drahtlose Lademodul vereinfacht zudem die Handhabung im Betrieb.
„Effizienz ist alles,“ fasst Christoph Münch zusammen. „Sie sparen Zeit bei der Einstellung der Parameter und reduzieren die Fehlerquote. Werden andere Regler immer komplexer und komplizierter in ihrer Bedienung, gehen wir den anderen Weg, ohne gleichzeitig auf Leistungsmerkmale zu verzichten. Beim blueMaster compact ist alles vorhanden, was der Anwender für Anwendungen benötigt und übersichtlich auf dem Smartphone, ob im Portrait- oder Landscape-Format, dargestellt. Die intuitive Bedienung ermöglicht es, sich ohne Einarbeitungszeit schnell zurecht zu finden. Und wird doch einmal Hilfe benötigt, hat der Benutzer aus jedem Menü direkten Zugriff auf eine Erklärung zu genau den Inhalten, die er gerade sieht.“
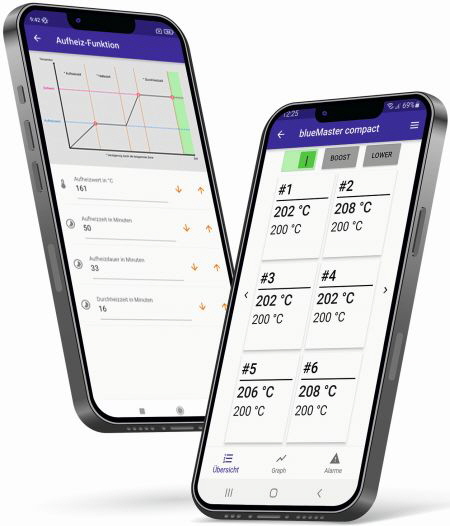 Intuitive Bedienung dank modernem Interface, grafischen Darstellungen und adaptiver Optimierung der Regelung.
Varianten für 3 und 6 Regelkreise verfügbar Die neuen Temperatur-Regelgeräte blueMaster compact sind für kleinere Anwendungen oder für den Einsatz im Servicebereich oder Laborbereich konzipiert. Sie verfügen über eine adaptive Optimierung der Regelung, d.h. sie passen ihr Regelverhalten ohne Benutzereingriff der angeschlossenen Last an und es ist keine Einstellung von PID-Parametern mehr nötig. Die Regelung bleibt selbst bei kleinsten Lasten stabil. Pro Zone stehen vier Betriebsarten (Regeln, Steuern, Leitbetrieb, Monitor) zur Verfügung. „Der neu entwickelte Regel-Algorithmus ist noch präziser und die automatische Adaptierung der Regelparameter garantiert eine sehr gute Regelqualität ohne Überschwinger,“ fasst es Christoph Münch zusammen. Die Geräte blueMaster compact sind wahlweise mit 3 oder 6 Regelkreisen verfügbar, haben viele Leistungsmerkmale einer großen Steuerung integriert, allerdings auf den Anwendungsbereich konzentriert und sind preislich attraktiv. „So vereint z.B. die Aufheizfunktion Rampe und Softstart und es gibt eine Selbstoptimierung der PID-Parameter,“ schließt Christoph Münch an.
Die Kunststoff-Gehäuse der Geräte blueMaster compact-Reihe sind äußerst kompakt gehalten und können so platzsparend an der Maschine oder im Umfeld platziert werden. Last- und Thermoanschluss sind auf einen 24-poligen Industriestecker gelegt und alle Sicherungen von außen zugänglich.
Energiekosten um 50 Prozent einsparen
Ressourcenschonung mit der „Blauen Düse“ In einem typischen Spritzgießbetrieb werden etwa 66 Prozent der eingebrachten elektrischen Energie den Produktionsanlagen zugeführt. Neben der Druckluftversorgung haben auch der Trocknungsprozess zur Aufbereitung von Granulaten oder die Kälteerzeugung für die Werkzeug- und Maschinenkühlung ihren Anteil am Ressourcenverbrauch. Deshalb sind die Betriebe der Kunststoffverarbeitung immer auf der Suche nach Optimierungsansätzen für den Energieeinsatz, auch in den Komponenten der Spritzgießwerkzeuge. Mit der Dickschichttechnologie von GÜNTHER Heißkanaltechnik können Unternehmen ihre Energieeffizienz um ein Vielfaches steigern.
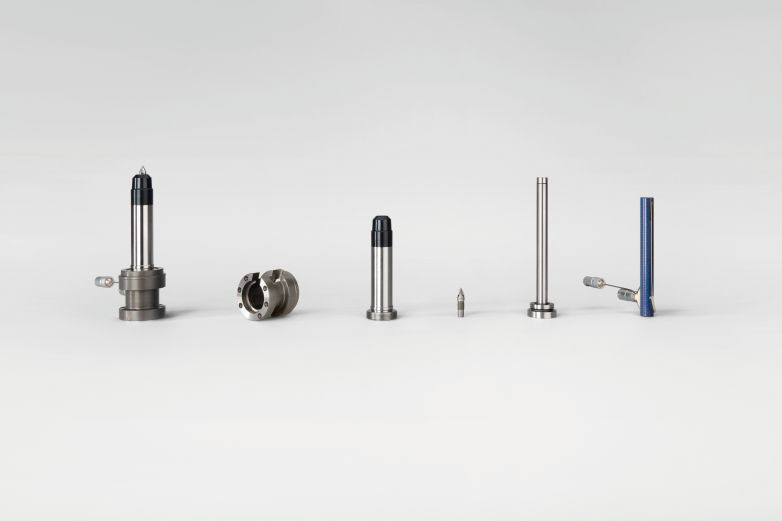 Die Forschungs- und Entwicklungstätigkeit für die Dickschichtheizer BlueFlow® haben zehn Jahre in Anspruch genommen.
Energieeffizienzpotenziale in der Werkzeugtechnik Wie lässt sich der Energieeinsatz optimieren? Hier denken viele sofort an elektrisch angetriebene Systeme, die fast 80 Prozent des gesamten Stroms in Industrie und Gewerbe verbrauchen. Bei Spritzgießmaschinen bietet sich ein großes Einsparpotenzial durch den Einsatz sogenannter vollelektrischer und elektromechanischer Antriebe. Es lohnt sich aber auch, einen Blick auf die aktuellen Entwicklungen der Werkzeugtechnik und deren einzelnen Komponenten zu werfen. Denn mit den Herstellungsmöglichkeiten und der wachsenden Vielfalt an Fertigungsverfahren steigen die Anforderungen an die Spritzgießwerkzeuge, wodurch diese weiter an Komplexität zunehmen werden.
Beim Thema „Effizienz“ hat GÜNTHER Heisskanaltechnik weitergedacht als viele Mitbewerber und sich schon früh als Vordenker einen Namen gemacht. Bereits zur K 2010 in Düsseldorf präsentierte der Technologieführer im Bereich Heißkanal- und Kaltkanaltechnik, eine revolutionäre, leistungsfähige und energieeffiziente Düsentechnologie. Siegrid Sommer, Geschäftsführerin bei GÜNTHER, beschrieb die Entwicklung der energieeffizienten Düsentechnologie auf Basis der Dickschichttechnik damals so: „Die Dickschichtheizer BlueFlow® für den Einsatz in den Heißkanaldüsen, haben insgesamt zehn Jahre intensiver Forschungs- und Entwicklungstätigkeit in Anspruch genommen. Mit der Standardisierung der Dickschicht-Technologie für Heißkanaldüsen haben wir etwas geschaffen, dass eine platzsparendere und energieeffizientere Heißkanalauslegung ermöglicht und nicht zu unterschätzende Energieeffizienzpotenziale eröffnet. Eigentlich müsste diese Düse nicht „Blaue“ sondern „Grüne Düse“ heißen.“ Gegenüber herkömmlichen Messingkörpern sind die Dickschicht-Heizelemente wesentlich filigraner und haben einen geringeren Durchmesser. Die Heizbahnen, die nur eine Dicke von ca. 20 µm aufweisen, lassen sich dank der Dickschicht-Technologie sehr viel enger und auch individueller pro Temperierzone aufbringen. So lässt sich die Temperaturverteilung in der gesamten Düse viel exakter steuern. Und - die BlueFlow®-Technologie lässt eine individuellere Heißkanalauslegung zu, wodurch man das Werkzeug kleiner/kompakter auslegen kann, was somit auch den Spritzgießprozess insgesamt effektiver gestaltet. Folglich können kleinere, leistungsangepasste Spritzgießmaschinen eingesetzt werden, ohne dass der Produktionsausstoß gemindert wird. Die Fertigung wird durchweg flexibler, gleichzeitig aber auch sehr viel energieeffizienter, was natürlich allen Spritzgießverarbeitern entgegenkommt, die auf Nachhaltigkeit und Energieeinsparungen setzen.
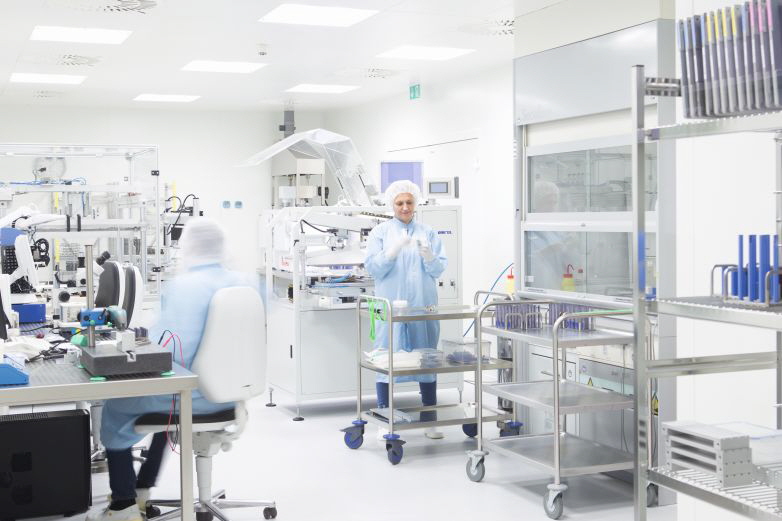 Mit der Standardisierung der Dickschicht-Technologie für Heißkanaldüsen wurde eine platzsparendere und energieeffizientere Heißkanalauslegung ermöglicht.
Technologieentwicklung bringt viele Vorteile Marco Kwiatkowski, Prokurist und bei GÜNTHER verantwortlich für die Abteilung Dickschicht, erklärt die Vorteile der Präzision bei der Wärmeverteilung: „Die Leistungsverteilung kann mit den neuen Dickschichtheizern praktisch auf den Millimeter genau erfolgen, was eine sehr viel homogenere Beheizung und damit bessere Aufbereitung der Kunststoffmasse ermöglicht. So ist beispielsweise eine hohe Leistungskonzentration im vorderen Düsenbereich realisierbar, was geringere Temperaturspitzen zur Folge hat und zu einer höheren Qualität der Schmelze führt.“
Dank der Dickschicht-Technologie lassen sich auch die Heizbahnen und damit die Heizung noch näher ans Material bringen. Sogar die Leistungsverteilung über das gesamte Heizrohr hinweg lässt sich viel freier und genauer gestalten, da die Leiterbahnen feiner (Breite/Durchmesser) und präziser (Abstände zwischen den Heizwindungen) positioniert werden können. GÜNTHER kann diese auch individuell entsprechend der Kavitätenauslegung anpassen. Die so optimierte und hohe Reproduzierbarkeit der Temperaturführung sowie die schnelle thermische Reaktion der BlueFlow®-Heißkanaldüse führen, verglichen mit konventionellen Düsenheizungen, zu einem geringeren Energieverbrauch. Durch das Senken der Verarbeitungstemperaturen kommt es zu reduzierten Zykluszeiten sowie zu erweiterten Verarbeitungsmöglichkeiten. Siegrid Sommer hält fest: „Das bedeutet, der Heiz- und Kühlaufwand im Werkzeug wird geringer, aufgrund der kleineren Nestabstände. Somit werden auch die Werkzeugabmessungen kompakter und der Einsatz von Spritzgießmaschinen mit weniger Leistung ist möglich. Die Produktion wird insgesamt flexibler und gleichzeitig viel energieeffizienter.“ Das Beispiel der BERGI-PLAST GmbH ist hierfür exemplarisch. Für den auf Kunststoffverarbeitung und Formenbau spezialisierten Kunststoffverarbeiter aus Bad Gottleuba-Berggießhübel, ist die ständige Analyse aller Prozessschritte bei der Spritzgießverarbeitung Grundlage für seine Ressourcen- und Energieeffizienz. Das Unternehmen ermittelte in einer Versuchsreihe die Werte für den Energieeinsatz in drei baugleichen 12-fach-Werkzeugen für die Fertigung von sog. „FlipTop“ für Tuben. Verarbeitet wurde Polypropylen (PP) mit einem Schussgewicht von ca. 8 Gramm, bei einer Zykluszeit von 12 Sekunden. Einer der eingesetzten Heißkanäle kam von GÜNTHER und war mit den Düsen BlueFlow® 4SHF80 ausgestattet. Bei dieser Düse mit BlueFlow®-Technologie ergab sich eine Energieeinsparung von 23 Prozent gegenüber der Heißkanaltechnik anderer Hersteller.
Einen weiteren Vorteil bringt das Material der Dickschichtheizungen. So kommt bei der herkömmlichen Düsen-Heiztechnik Magnesiumoxid als elektrische Isolierung um den stromführenden Heizdraht zum Einsatz. Da dieses Material hygroskopisch ist, also Feuchtigkeit aus der Umgebung (meist in Form von Wasserdampf aus der Luftfeuchtigkeit) bindet, wird die Düsen-Heiztechnik langsam auf 100 °C hochgeheizt. Anschließend muss zur Wasserdampfaustreibung aus den Heißkanalsystemen eine Heizruhephase eingelegt werden. Dies wiederum ist zeit- und energieintensiv. Da die Dielektrium- und Leiterbahnen-Schichten der Dickschichtheizer nicht hygroskopisch sind, entfällt das „Hochheizen“ und spart daher Energie. Und auch die Heizruhephase entfällt, was wiederum Zeit spart. Vergleichsmessungen mit herkömmlichen Heißkanaldüsen ergaben eine Energieein- sparung um bis zu 50 Prozent beim Fahren der Maschine mit der niedrigsten Verarbeitungstemperatur.
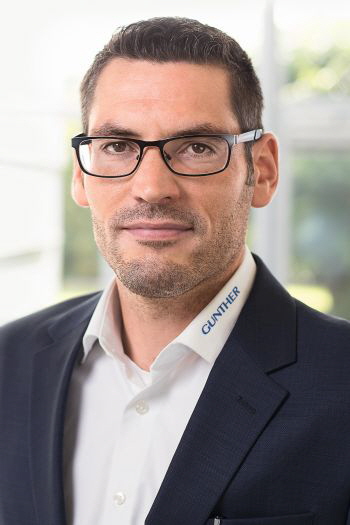 „Die Leistungsverteilung kann mit den Dickschichtheizern auf den Millimeter genau erfolgen“, erklärt Marco Kwiatkowski, Prokurist und bei GÜNTHER verantwortlich für die Abteilung Dickschicht.
Erhebliche Einspar-Vorteile in der täglichen Praxis Zusammenfassend kann man sagen, dass sich dank der technischen Features der BlueFlow®-Technologie in der täglichen Praxis erhebliche Vorteile sowohl für die Werkzeugbauer als auch für die Spritzgießverarbeiter ergeben. Die insgesamt kleinere Baugröße der BlueFlow®-Düse ermöglicht neben engeren Nestabstände auch größere Freiheitsgrade beim Verlegen der Kühlkanäle und eine höhere Designfreiheit bei der Teileauslegung. Deshalb sollten neue Werkzeuge von Anfang an mit den Dickschichtheizern bzw. den entsprechenden Düsensystemen von GÜNTHER ausgestattet oder ältere Spritzgießwerkzeuge mit der BlueFlow®-Technologie nachgerüstet werden. Für den Spritzgießverarbeiter wirkt sich zudem der Einsatz kleinerer Spritzgießmaschinen auf die Betriebskosten aus und damit auch auf den Energieverbrauch.
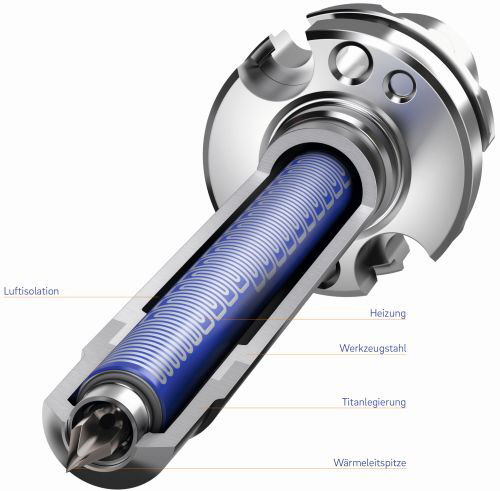 Da die Dielektrium- und Leiterbahnen-Schichten der Dickschichtheizer nicht hygroskopisch sind, entfällt das Hochheizen der Düsen und spart daher Energie.
BlueFlow®-Technologie auf einen Blick
Technische Vorteile
|
Kundennutzen
|
kleinere Baugröße
kleiner Schaftdurchmesser
enger Nestabstand
|
Kleinere Spritzgussmaschinen und damit ein geringerer Invest.
Geringere Betriebskosten aufgrund geringerem Energieverbrauch.
Weniger Materialkosten für die Werkzeugform, leichteres Handling.
Höherfachige Werkzeuge bei vergleichbarer Baugröße des Werkzeugs, bedeuten mehr Teile pro Werkzeug.
Mehr Freiheitsgrade für den Kühlungsverlauf, dadurch höhere Teilequalität.
Größere Designfreiheit der Teile bei Direkteinspritzung.
|
Bessere Temperaturführung
|
Höhere Qualität der Teile.
Reduzierung der Ausschussquote.
Kosteneinsparung beim Energieverbrauch.
Reduktion der Zykluszeit durch Senkung der durchschnittlichen Schmelztemperatur und dadurch Reduktion der Produktkosten.
Verarbeitung von thermisch sensiblen Kunststoffen (z.B. Halogenfreier Flammschutz)
|
Schnelle thermische Reaktion
|
Reduktion der Zykluszeit, weil die Möglichkeit besteht, schneller einzuspritzen.
Effizienzsteigerung
Höhere Qualität der Schmelze wegen geringerer Temperaturspitzen.
Höhere Prozessstabilität und damit Reduktion der Ausschussquote.
|
Nicht hygroskopisch
|
Reduktion der Ausfallwahrscheinlichkeit durch Feuchtigkeit.
|
Hohe Spannungsfestigkeit
|
Geringere Ausfallwahrscheinlichkeit aufgrund von Spannungsspitzen und dadurch erhöht sich die Standzeit (geringe Stillstandsquote)
|
Besuchen Sie uns auf der Swiss Plastics Expo. Wir freuen uns auf Ihren Besuch an unserem Stand: Halle 2 / Stand A 2016 |