Die Hansgrohe Group gilt nicht nur als führender Hersteller von Premiumprodukten für Bad und Küche, sondern auch als Vorreiter bei der technologischen Umsetzung von Nachhaltigkeitsprinzipien. Ein aktuelles Beispiel dafür ist die Inbetriebnahme einer vollautomatisierten Recyclinglinie für die Verarbeitung metallisierter Fehlteile aus der Spritzguss-Produktion im Werk Offenburg. Entwickelt wurde sie in enger Zusammenarbeit mit den Hochspannungsexperten von ImpulsTec und dem Mühlenbauer GETECHA. Dank der innovativen Anlage lässt sich derzeit ein fast lückenloser Rohstoffkreislauf realisieren.
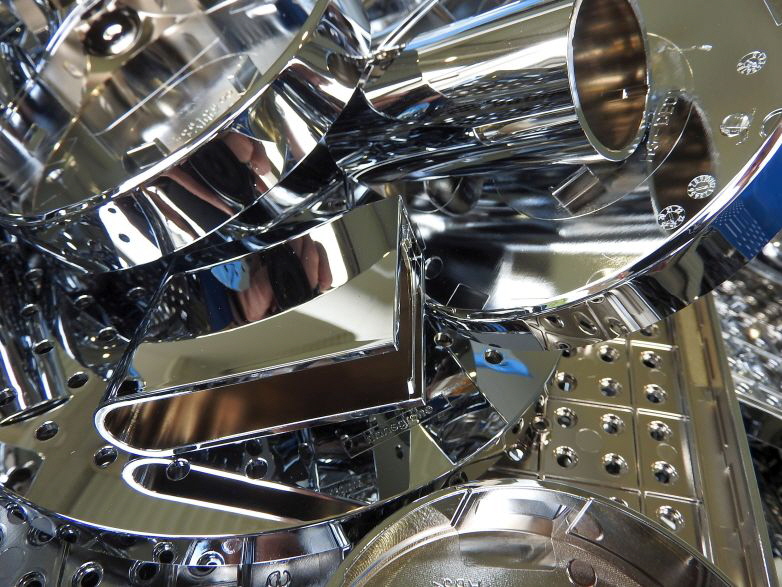 Dank der hochinnovativen Anlage für das Recycling galvanisierter Fehlteile aus ABS kann Hansgrohe derzeit fast 98 Prozent seiner Rohstoffe wiederverwenden.
Seit geraumer Zeit schon vertrauen die Verantwortlichen bei Hansgrohe auf Zerkleinerungstechnik von GETECHA. Auch als es für Projektleiter David Zapf im vergangenen Jahr darum ging, in seiner Funktion als Specialist Surface Technology von Hansgrohe die Grundlagen für die Entwicklung einer neuen Recyclinganlage zur Wiederaufbereitung chromatierter Fehlteile aus der Spritzguss-Produktion zu schaffen, kamen wieder Systemlösungen des deutschen Mühlenbauers zum Einsatz. Diesmal waren es eine energieeffizient arbeitende Schneidmühle vom Typ RS 30060 sowie eine Absauganlage GA 500 S, die sich nach verschiedenen Testläufen als Ideallösung für die neue Rückgewinnungslinie erwiesen. Sie decken die Prozessstufen der Vorzerkleinerung und der Mahlgut-Reinigung (inklusive Abluftfilterung) ab. Ihre Performance hat entscheidende Bedeutung für das Qualitätsniveau, dass sich bei der anschließenden Entschichtung der Spritzgussteile und der Trennung der Rohstoffe in einen Anteil Kunststoff – in diesem Fall ABS – und einen Anteil Metall – hier ein Mix aus Nickel, Kupfer und Chrom – erzielen lässt.
Rohstoffe direkt wiederverwerten Die Chromatierung der Feuchtraum-Produkte (z.B. Duschköpfe) dient nicht nur ihrer optischen Veredelung, sondern auch ihrem Werterhalt, da sie die Oberflächen vor Korrosion und mechanischer Beschädigung schützt. Meist handelt es sich dabei um eine nur etwa 40 µm dünne Schicht, die bis zu 15 Prozent des Produktgewichts ausmachen kann. Allerdings überstehen bei Hansgrohe nur Spritzgussteile mit absolut makelloser Chromatierung die strenge Qualitätssicherung der Galvanik, weshalb routinemäßig ein stetes Volumen an Fehlteilen anfällt. In Anbetracht der guten Erfahrungen, die das Unternehmen bereits bei seinen Inhouse-Rohstoffkreisläufen für nicht metallisierten Ausschuss sammeln konnte, entstand nun vor etwa zwei Jahren der Wunsch, einen solchen Zyklus auch für die verchromten ABS-Formteile zu etablieren. Klare Zielsetzung war es hierbei laut David Zapf, „die beschichteten Produkte so zu entmetallisieren, dass der Anteil an Kunststoff wieder der eigenen Neuteileproduktion zugeführt werden kann, während sich der hochkonzentrierte metallische Anteil am Markt veräußern lässt.“
Um dieses Vorhaben zu verwirklichen, intensivierte der Oberflächenexperte nicht nur die Zusammenarbeit mit GETECHA, sondern holte auch das Hightech-Unternehmen ImpulsTec ins Boot. Der Grund: Auf Basis der Hochspannungsimpulstechnik hat der Radebeuler Sondermaschinenbauer ein vielbeachtetes Verfahren entwickelt, das es unter anderem ermöglicht, metallische Dünnschichten von verchromten ABS-Bauteilen durch eine elektrohydraulische Schockwellen-Behandlung zu separieren. Eine wichtige Voraussetzung dafür, dass hierbei ein optimaler Wirkungsgrad erzielt wird, ist die prozesssichere Zerkleinerung der galvanisierten Fehlteile zu einem Mahlgut mit homogener Korngröße und geringem Staubanteil. „Nach und nach konkretisierte sich daher unser Plan von der neuen Recyclinganlage als einer hochgradig automatisierten Verarbeitungslinie, bei der die kontinuierlich zugeführten Fehlteile primär drei Prozessstufen durchlaufen: Zunächst eine systematische Vorzerkleinerung mit Staubabsaugung, anschließend die Abspaltung der Chromschicht im Schockwellen-Verfahren, und letztlich die magnetische Trennung, so dass wir zwei sortenreine Kunststoff- und Metallfraktionen erhalten, die wir einerseits der Granulierung und andererseits der Vermarktung zuführen können“, berichtet David Zapf.
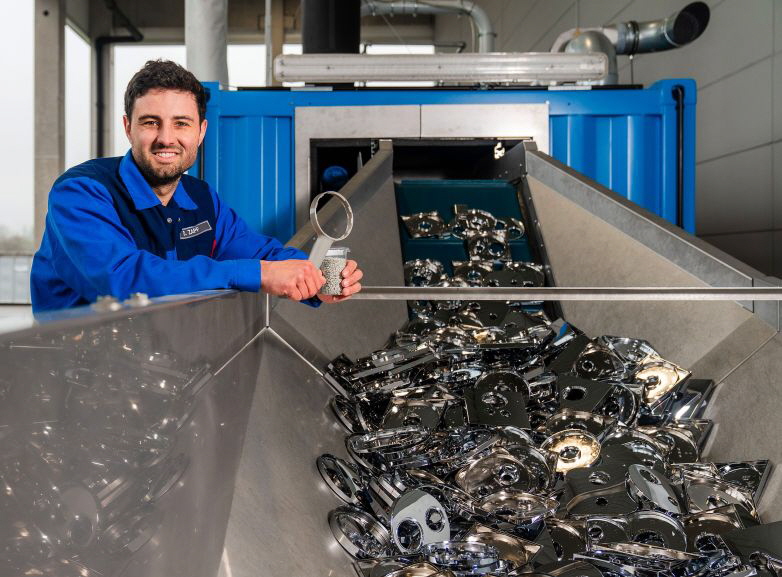 Für die Realisierung der neuen Recyclinganlage intensivierte David Zapf nicht nur die Zusammenarbeit mit GETECHA, sondern holte auch das Hightech-Unternehmen ImpulsTec ins Boot.
Mühle und Absaugung aus einer Hand Wie schon bei früheren Vorhaben legte der Projektmanager von Hansgrohe maßgebliche Bereiche der Prozessstufe rund um die Vorzerkleinerung in die Hände von GETECHA. Das bedeutet, dass der Aschaffenburger Anlagenbauer nicht nur die Schneidmühle – hier eine RotoSchneider RS 30060 – bereitstellte, sondern auch das Entstaubungs- und Abluftsystem für die Mahlgutreinigung. „Das erwies sich als optimal. Denn daran konnten wir direkt mit den prozesstechnischen Komponenten unserer materialselektiven elektrohydraulischen Schockwellen-Technologie – etwa dem Flüssigmedium-Reaktor – anknüpfen. Zugleich war damit von Beginn an sichergestellt, dass unser Verfahren stets mit bestens konditioniertem Mahlgut arbeiten kann“, betont Stefan Eisert, der Geschäftsführer von ImpulsTec.
Bei der RS 30060 von GETECHA handelt es sich um eine modular konzipierte, kompakte Trichtermühle mit einer 640 x 410 mm großen Mahlkammeröffnung und einem Rotorschneidkreis von 300 mm. Nach dem Scherenschnitt-Prinzip zerkleinern hier 3 x 2 Rotor- und zwei Statormesser die zugeführten Fehlteile, die Durchmesser von bis zu 500 mm und Wandstärken von bis zu 8,0 mm haben dürfen. Der Rotor dreht mit etwa 420 min-1 und wird von einem 15 kW-Drehstrommotor in IE3-Ausführung angetrieben. Zu den besonderen Qualitätsmerkmalen der Schneidmühle gehören unter anderem die außen liegende Rotorlagerung, die ein maßgebliches Sicherheitsplus darstellt, und die geometrische Präzision des Schneidkreises, die ein konstant homogenes Zerkleinerungsergebnis gewährleistet. Weitere konstruktive Highlights sind der segmentierte Rotoraufbau, die massive Riemenscheibe – sie sorgt für zusätzliche Schwungmasse – und die insgesamt gute Zugänglichkeit aller wichtigen Komponenten.
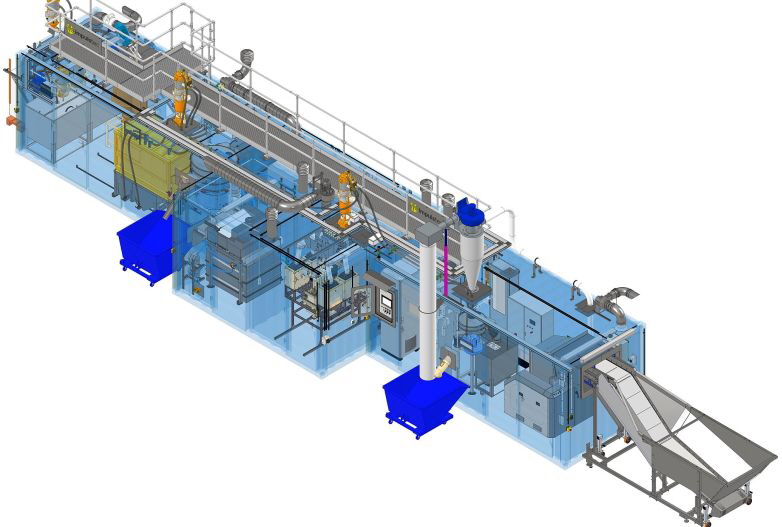 Die neue Recyclinganlage ist eine automatisierte Verarbeitungslinie, bei der die galvanisierten Fehlteile zunächst eine Vorzerkleinerung mit Staubabsaugung, anschließend ein Schockwellen-Verfahren, und letztlich die magnetische Trennung durchlaufen.
Maßgeschneiderte Prozesslösung Für den Einsatz in der neuen Recyclinganlage von Hansgrohe bestückte GETECHA die Mühle mit speziellen Schneidmessern, deren Schnittgeometrie exakt auf die zerkleinerungstechnischen Anforderungen von beschichteten Kunststoffen abgestimmt ist. Außerdem wurde sie rund um das Mahlgehäuse mit einer integrierten Schalldämmverkleidung mit doppelwandigem Dämmmaterial ausgekleidet und in einer Lärmschutzkabine auf vier Schwingelementen aufgestellt. Zur Wartung und Reinigung lassen sich Trichter und Mahlraum einfach mit einer Spindel öffnen und per Schnellverschluss verriegeln. Während die Statormesser nach dem Schleifen oder Tausch mit wenigen Handgriffen am Festanschlag montiert sind, können die Rotormesser bequem in der mitgelieferten Lehre voreingestellt werden, so dass der Schnittspalt stets stimmt. Die Entnahme des Lochsiebs (6 mm Rundlochung) erfolgt werkzeuglos. Sämtliche Oberflächen sind allseitig bearbeitet und glatt, damit sich sie leicht pflegen lassen. „All das reduziert den Aufwand für die Instandhaltung der Schneidmühle und stellt ihre hohe Verfügbarkeit sicher“, betont Andreas Lanz, Gebietsvertriebsleiter von GETECHA.
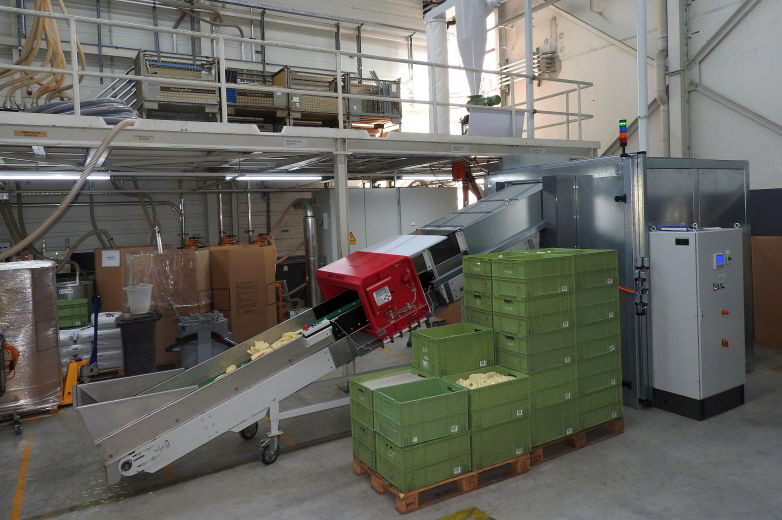 GETECHA lieferte die gesamte Prozessstufe der Vorzerkleinerung der neuen Recyclinganlage von Hansgrohe, bestehend aus Schneidmühle, Förderbandsystem sowie Entstaubungs- und Abluftsystem.
Steuerungstechnisch integriert Auch steuerungstechnisch fügt sich die GETECHA-Mühle homogen in das Gesamtgefüge der Recyclinganlage ein. Um beispielsweise die kontinuierliche Materialzuführung zu gewährleisten und eine Überfüllung der Mahlkammer auszuschließen, wird das dafür eingesetzte Förderband mit den einlaufenden Fehlteilen und Angüssen über die lastabhängige Steuerung der Schneidmühle geregelt. Darüber hinaus werden Produktions- und Anlagenzustand der Schneidmühle kontinuierlich überwacht und eine optische Anzeige signalisiert den jeweiligen Betriebsmodus. In toto werden alle Prozesse automatisch erfasst und über ein mobiles Datennetz an den Betreiber der Anlage übermittelt. Die Schneidmühle verfügt über einen integrierten Schaltschrank mit leicht verständlichen Bedienelementen.
Je nach Material und Beschickung ist die RS 30060 von GETECHA für einen Stundendurchsatz von bis zu 400 kg ausgelegt und zerkleinert die verchromten ABS-Formteile – je nach Lochung des Siebes – zu einem Mahlgut mit Korngrößen von beispielsweise 5,0 mm. In der Recyclinganlage von Hansgrohe wird das Mahlgut anschließend mit der Absauganlage GA 500 S von GETECHA aus dem Siebwagen der Mühle abgesaugt und in einem Zyklon abgeschieden. Dabei stellt eine Zellenradschleuse sicher, dass das Mahlgut lufttechnisch getrennt und druckneutral ausgetragen wird. Das integrierte Filtersystem – ebenfalls von GETECHA – reinigt die Abluft und führt sie wieder der Umgebung zu. Im weiteren Prozess erfolgen die Trennung des Kunststoffs von den metallischen Anhaftungen im Stoßwellen-Verfahren von ImpulsTec sowie die Separierung und Trocknung der beiden Werkstoff-Fraktionen.
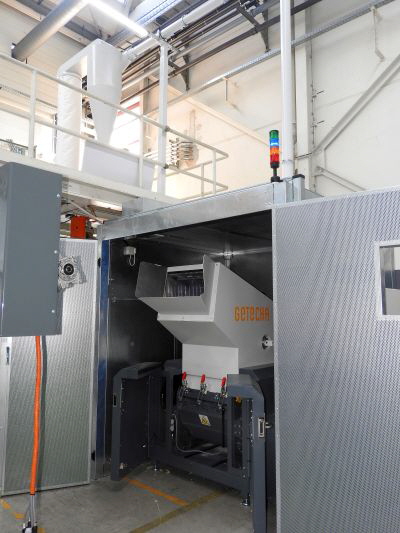 Für den Einsatz in der Recyclinganlage von Hansgrohe stattete GETECHA seine Trichtermühle RS 30060 mit einem Mahlgehäuse mit integrierter Schalldämmverkleidung und einer Lärmschutzkabine aus.
Hochinnovativ mit viel Potenzial Als die Recyclinganlage Mitte 2024 in Betrieb ging, war allen Beteiligten klar: Hier handelt es sich um eine hochinnovative und vielleicht sogar bislang einzigartige Systemlösung. Dank der neuen Aufbereitungslinie kann Hansgrohe aktuell fast 98 Prozent seiner Rohstoffe wiederverwenden. „Zum einen erhalten wir eine hochkonzentrierte Metallfraktion, die vorrangig Kupfer und Nickel enthält und zur Verhüttung in den Verkauf geht. Diese Wertstoffe werden also zu 100 Prozent wieder dem Rohstoffkreislauf zugeführt. Zum anderen erhalten wir das entschichtete ABS, dass wir zur Herstellung von Neuteilen einsetzen. Damit schließen wir den Wertstoffkreislauf am Standort“, sagt Pascal Dengler, der für den reibungslosen Betrieb der Recyclinganlage verantwortlich ist.
Übrigens: Da das neue Recyclingsystem auf die Entmetallisierung von bis zu jährlich 100 Tonnen verchromtem Kunststoff ausgelegt ist, ermöglichte es Hansgrohe inzwischen die Realisierung einer Handbrausen-Produktlinie für die Premiummarke hansgrohe, bei der ausnahmslos rezykliertes Granulat verwendet wird.
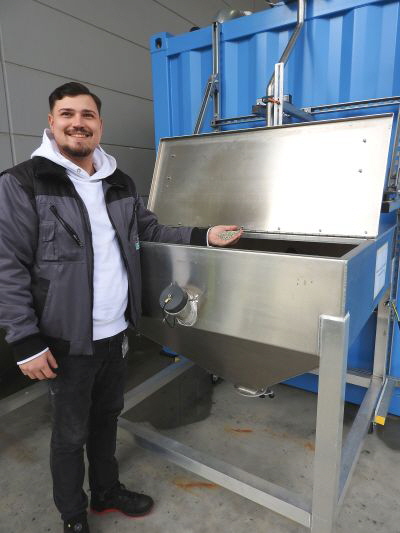 Pascal Dengler: „Neben einer hochkonzentrierten Metallfraktion erhält Hansgrohe aus seiner neuen Recyclinganlage einwandfrei entmetallisiertes ABS, das wieder zur Herstellung von Neuteilen eingesetzt wird.“
Firmenprofil: Kundenorientierte Individualisierung als Standard Die Getecha GmbH wurde 1956 gegründet und hat ihren Stammsitz in Aschaffenburg. Das Familienunternehmen beschäftigt derzeit 40 Mitarbeiter, hat eine Niederlassung in den USA. Die Geschäftsführung liegt in den Händen von Christine Rosenberger.
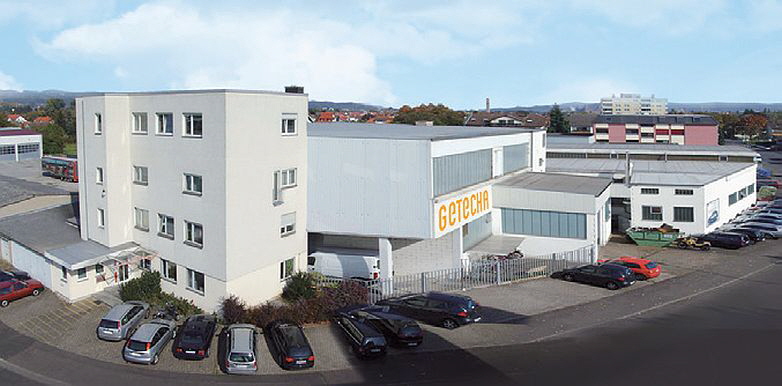 Der Hauptsitz von GETECHA in Aschaffenburg
Getecha entwickelt und produziert Kunststoff- und Verbundstoff-Schneidmühlen für den dezentralen und zentralen Einsatz, innovative Angussentnahme-Systeme sowie komplette Automationslösungen für die Prozesse Zuführen, Einlegen, Entnehmen, Verpacken und Palettieren sowie Mahlgutförderung und BigBag-Befüllung.
In Deutschland zählt das Unternehmen zu den führenden Herstellern von Zerkleinerungssystemen für die Kunststoff verarbeitende Industrie. Zu den Kunden von Getecha gehören die Anwender und Maschinenbauer der Spritzgieß-, Extrudier-, Blasform- und Thermoformtechnik. Auch für die Automatisierer der Kunststoff- und Recyclingindustrie ist das Unternehmen ein kompetenter und häufig frequentierter Projektpartner. Die Anlagen und Systemlösungen von Getecha kommen weltweit zum Einsatz.
Download Imagebroschüre Getecha (PDF-Datei, 4,4 MB)
Firmenvideo
Produkte
Für mehr Informationen bitte auf die untenstehenden Links klicken: Zerkleinerung • Beistellmühlen • Zentralmühlen • Großmühlen • Einzugsmühlen • Vorschneider • Zubehör
Automation • Verpackungslösungen für Flaschen • Verpackungslösungen für Kanister • Sonderautomationen |