Inhaltsangabe: • Möglichkeiten und Bauteileigenschaften im Pulver-Bett – Verfahren (PBF-LB) • Lokaler Verschleißschutz durch Laserauftragschweißen (DED) • Laserdispergieren von Hovadur® Kupferlegierung – erste Erfahrungen
Zusammenfassung Kupferlegierungen und insbesondere ausscheidungshärtende Kupferlegierungen sind aufgrund ihrer hohen Reflektivität eine echte Herausforderung für die Verarbeitung über Lasertechnologien, da hier in den allermeisten Fällen rote Laser im Einsatz sind. Die Schmelzmetall AG und die deutsche Tochter, die Schmelzmetall Deutschland GmbH, entwickeln im Rahmen ihrer technologieorientierten strategischen Ausrichtung seit mehr als 13 Jahren anspruchsvolle FuE-Projekte. Dabei handelte es sich zunächst um Oberflächenveredelungen von Bauteilen, wobei die Lasertechnik durch Forschungsinstitute eingebracht und um die additive Fertigung kompletter Bauteile erweitert wurde. 2019 erfolgte die Investition in eine eigene Anlage zum 3D-Drucken von Bauteilen aus Kupferlegierungen. Neben der Entwicklung der Prozessparameter für den Pulver-Bett-Prozess (PBF-LB) wurden unterschiedliche Wärmebehandlungsstrategien entwickelt, um auf die Anforderungen der Anwendung angepasste Eigenschaften einstellen zu können. Hierbei wurde die Aufbaurichtung berücksichtigt und die Eigenschaften in Abhängigkeit der Aufbaurichtung ermittelt. Somit können Bauteile so im Bauraum orientiert werden, wie es für die Funktion der Bauteile optimal ist. Der Prozess des Laserauftragschweißen wird eingesetzt, um gezielt Bauteile die konventionell aus einer Hovadur®-Legierung hergestellt werden, lokal dort verschleißgeschützt auszuführen, wo es für die Funktionalität des Bauteils notwendig ist und die Standzeiten der Bauteile deutlich verbessert werden. Somit können unterschiedliche Eigenschaften, wie hohe Wärmeleitfähigkeit oder elektrische Leitfähigkeit mit guter Verschleißbeständigkeit kombiniert werden. Die Möglichkeiten des DED-Prozesses werden anhand von Anwendungsbeispielen erläutert. Beim Laserdispergieren geht es darum Hartstoffpartikel aus Wolframschmelzkarbid oder Niobcarbid mittels Laser in die Oberfläche einzubringen. Am Beispiel eines Druckgusskolben wird aufgezeigt welcher Volumenanteil in der Oberfläche eingebracht werden kann, und welchen Einfluss dieser Prozess auf die Erhöhung der Lebensdauer hat und wie sich der Prozess auf die Herstellkosten und damit die Wirtschaftlichkeit auswirkt.
Die Motivation Was veranlasst ein Mittelständiges Unternehmen sich mit den additiven Fertigungsverfahren auseinander zu setzen? Dabei stehen zwei Anwendungsfelder unserer Hovadur®-Legierungen im Vordergrund. Zum einen der Kunststoff-Formenbau und zum anderen die Luft- und Raumfahrt.
Geht es in dem ersten Bereich um das Thema Zykluszeit, und damit um die wirtschaftliche Herstellung von Spritzguss-Produkten, so ist man sehr schnell damit konfrontiert, wie man die Kühlung so nah wie möglich an die Kavität bringt. Innere Kühlkanäle sind hier eine Lösung, die nur durch den Metall-3Druck realisiert werden können. In der Raumfahrt geht es darum, wesentliche Antriebskomponenten, wie Brennkammern möglichst funktionsoptimiert, schnell und kostengünstig zu fertigen.
Motiviert und Getrieben durch die Entwicklungen in diesen Anwendungsfeldern haben wir früh, bereits 2009 damit begonnen, eigene öffentlich geförderte F&E-Projekte aufzusetzen oder uns an geeigneten F&E-Projekten bzw. uns in sogenannten projektbegleitenden Ausschüssen zu beteiligen.
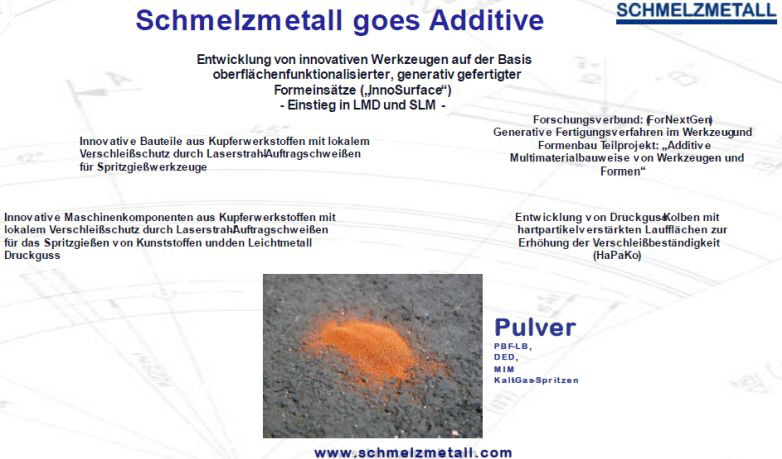 Auszug aus verschiedenen F&E-Projekten
PBF-LB, Metall 3D-Druck Ein wesentliches Ziel als Voraussetzung für Fertigung von Prototypen oder Serienbauteilen ist die sichere Verarbeitbarkeit von Hovadur®-Kupferlegierungen im PBF-LB – Verfahren. Um dieses Ziel zu erreichen, muss die gesamte Fertigungskette vom Pulver bis zum Fertigteil entwickelt werden. Als Zielkriterium wird bei der Schmelzmetall eine Dichte von 99,5% der theoretischen Dichte angesetzt. Einflussfaktoren, die sehr detailliert aufeinander abzustimmen sind, und sich gegenseitig beeinflussen sind: Laserleistung, Belichtungsge- schwindigkeit, Verhältnis belichtete Fläche zu Bauraum, Spurabstand, Schichtdicke, Belichtungsstrategie, Energiedichte als Faktor aus Laserleistung-Belichtungsgeschwindigkeit und Schichtdicke, Bauraumtemperatur, Schutzgas-Strömung, Laserfokus-Durchmesser, Energieverteilung im Laserfokus, Korngrößenbereich- und Verteilung des eingesetzten Pulvers. Diese Aufzählung erhebt keinen Anspruch auf absolute Vollständigkeit und kann ergänzt werden um Einflussfaktoren, die eine Abhängigkeit zur Anlage selbst haben, wie z.B. Eintrittswinkel des Laserstrahls zum Schutzgasstrom, der Schutzgasstrom selbst. Die Dichte wird sowohl nach dem Archimedischen Prinzip und parallel mikroskopisch ermittelt.
Bei den angestrebten Hovadur®-Kupferlegierungen handelt es sich um sogenannte ausscheidungshärtende Legierungen. Diese Legierungen werden zur Einstellung der gewünschten erzielbaren Eigenschafen einer zweistufigen Wärmebehandlung unterzogen. In der ersten Stufe werden diese Legierungen lösungsgeglüht. Dies erfolgt durch Tempern bei einer bestimmten Temperatur -je nach Legierung 850-950°C- und anschließendem Abschrecken in bewegtem Wasser. Hierbei werden alle metastabilen Gefüge-Ausprägungen in Lösung genommen. In der zweiten Stufe wird durch Tempern bei 300–550°C über einen Zeitraum mehrerer Stunden Phasen ausgeschieden und so die Eigenschaften eingestellt. Für gedruckte Bauteile liegen die Wärmebehandlungsbedingungen abweichend von denen für konventionell gefertigte Halbzeuge und müssen so neu bestimmt werden.
Um den Prozess wirtschaftlich zu gestalten, stellte sich die Frage, ob auf die erste Stufe der Wärmebehandlung verzichtet werden kann. Nimmt man an, dass der Bauprozess eine Art Lösungsglühung bereits darstellt, der Laser bringt lokal eine hohe Energie ein, das Material wird lokal begrenzt aufgeschmolzen und bedingt durch die hohe Wärmeleitfähigkeit des umliegenden Materials wieder sehr schnell abgekühlt (abgeschreckt). Je nach Anwendung steht die Festigkeit oder die höchste Wärmeleitfähigkeit bzw. elektrische Leitfähigkeit im Vordergrund. Oder der Anwender wünscht sich basierend auf den Anforderungen, denen er sich gegenübersieht, den bestmöglichen Kompromiss der Eigenschaften. Mit Ausnahme der Einstellung der höchsten elektrischen Leitfähigkeit wird für die höchste Härte und Festigkeit bzw. den besten Kompromiss die Wärmebehandlung einstufig ausgeführt. Härte und Leitwert können wir intern bestimmen, andere Kennwerte werden extern über akkreditierte Labore ermittelt.
Die folgende Tabelle zeigt die ermittelte Härte und elektrische Leitfähigkeit für die Legierung Hovadur® CNCS an Probekörper wie Würfel mit 25 mm Kantenlänge und an Zugproben (grün). Dies für die von uns entwickelten 3 Wärmebehandlungsoptionen und im Vergleich zu den Datenblatt-Werten für geschmiedete Halbzeuge (rot).
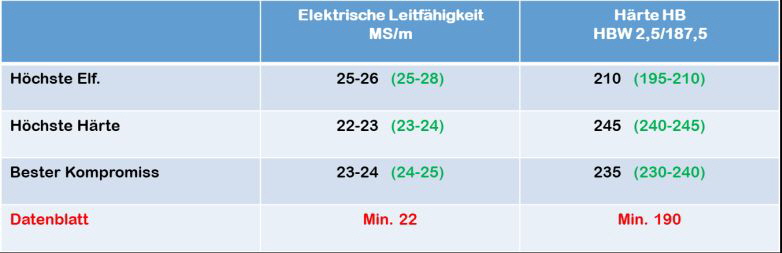 Bild 2: Kennwerte für gedruckte Bauteile aus Hovadur® CNCS
Zur Ermittlung der mechanischen Kennwerte werden die Zugproben unter unterschiedlichen Winkel aufgebaut, im Einzelnen unter 0 Grad (liegend); unter 45 Grad und 90 Grad (stehend).
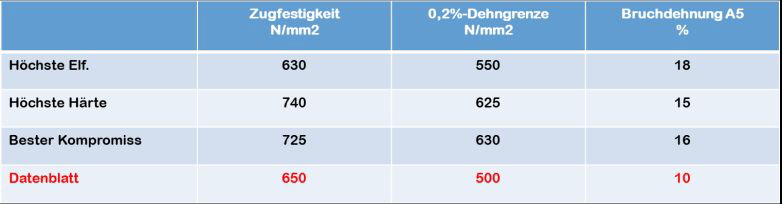 Bild 3: Mechanische Kennwerte für gedruckte Bauteile aus Hovadur® CNCS
In der Tabelle aus Bild 3 sind die Mittelwerte aus je Baurichtung 5 Proben angegeben. Besonders positiv ist, dass die Dehnung immer deutlich über der Dehnung geschmiedeter Halbzeuge liegt. Die folgende Tabelle (Bild 5) zeigt die ermittelten Kennwerte in Abhängigkeit zur Orientierung im Bauraum.
Diese Kenntnis der orientierungsabhängigen Eigenschaften gibt uns die Möglichkeit, das Bauteil – so die Abmessungen des Bauteils und der zu Verfügung stehende Bauraum dies zulassen- das Bauteil so im Bauraum auszurichten und zu drucken, das wir für die Anwendung und Belastung des Bauteils besten Eigenschaften einstellen können.
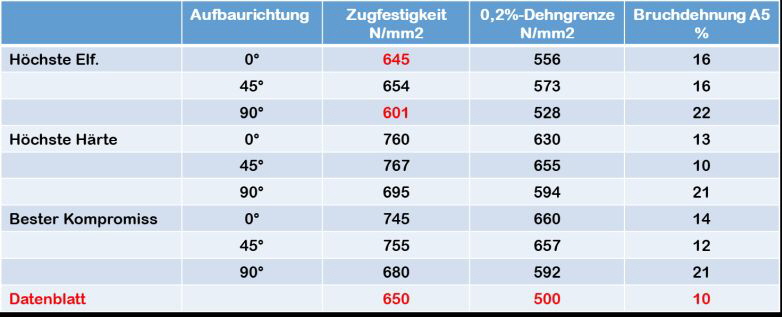 Bild 4: Mechanische Kennwerte für gedruckte Bauteile aus Hovadur® CNCS in Abhängigkeit der Aufbaurichtung
Im Kunststoff-Formenbau sind wir immer wieder mit der Fragestellung konfrontiert, wie die über den Kunststoff eingebrachte Wärme möglichst schnell verteilt wird, um eine gleichmäßige Werkzeugwandtemperatur einzustellen, um sogenannte Hot-Spots zu vermeiden, und im zweiten Schritt die Wärme so schnell wie möglich abzuführen. Ein sehr hoher Anteil am Spritzgusszyklus hat die Abkühlung von Einspritz- auf Entformungstemperatur. Neben der hohen Wärmeleitfähigkeit durch den Grundwerkstoff spielt hier die konturnahe Kühlung eine entscheidende Rolle. Die folgende Darstellung zeigt einen Formkern in konventioneller Ausführung und mittels PBF-LB mit optimierter Kühlung gefertigt.
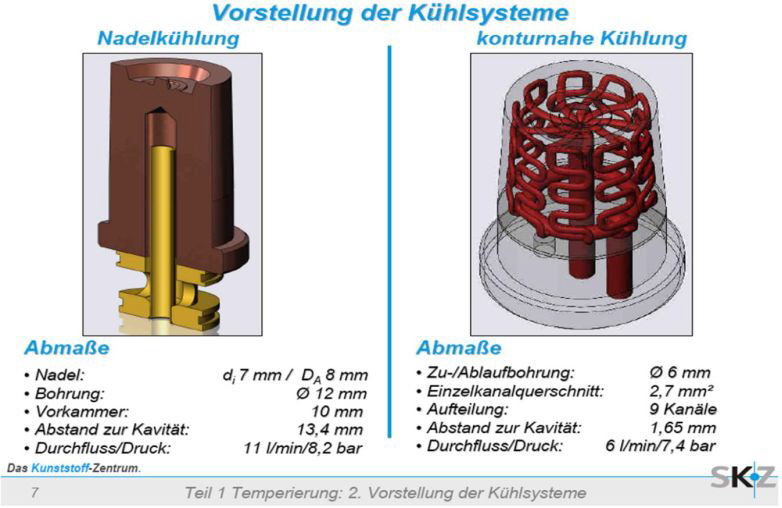 Bild 5: Formkern, konventionell und mit konturnaher Kühlung
Die Arbeiten beruhen auf eine Verbundprojekt mit dem SKZ, Fraunhofer-ILT und verschiedenen Industriepartner. Ermittelt wurde der kürzet mögliche Spritzguss-Zyklus für einen konventionell gefertigten Formkern aus einem Werkzeugstahl. Mittels Thermokamera wurde dann für die weitern Formkerne die Temperatur am entformten Spritzteil gemessen.
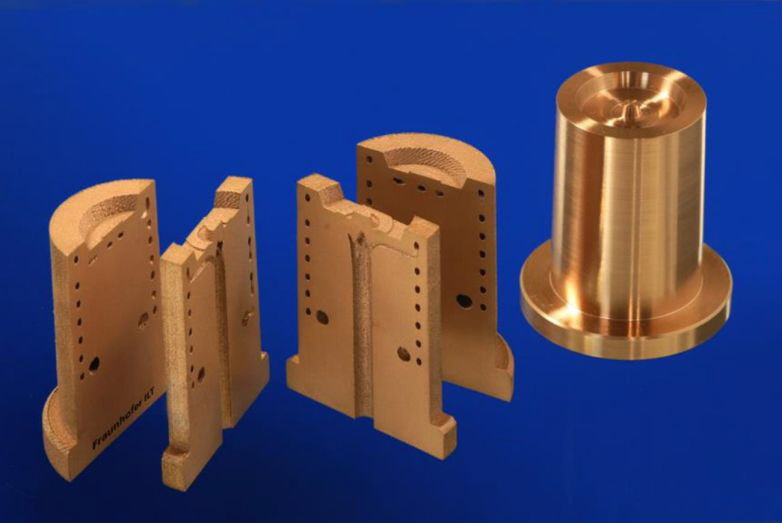 Bild 6: Formkern und Schnittmodel aus Hovadur® CNCS
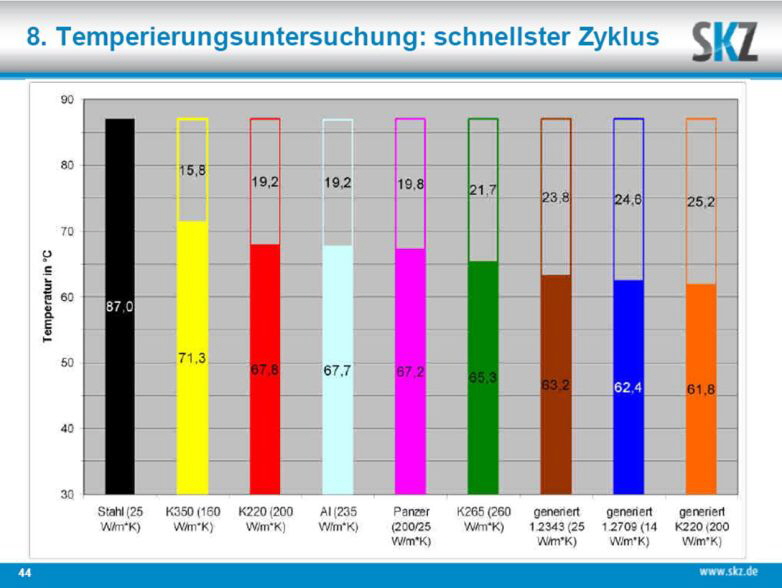 Bild 7: Temperaturen am entformten Spritzteil für verschiedene Formkerne
Die Grafik zeigt sehr deutlich den Einfluss der hohen Wärmeleitfähigkeit des gewählten Grundwerkstoffes für den Formkern und den Einfluss der konturnahen Kühlung. Vergleicht man den Formkern konventionell gefertigt aus der Legierung Hovadur® CNCS (K220) mit dem mittels PBF-LB gefertigten, so zeigt sich, dass die Zykluszeit um weitere 10% reduziert werden kann. Für den Spritzgießer ergeben sich somit auch klare wirtschaftlichen Vorteile. Da die Fertigung von Prototypen oder Serienbauteilen mittels PBF-LB nach wie vor eine teure Fertigung im Vergleich zur konventionellen Fertigung darstellt, haben wir uns der Herausforderung gestellt und sind dem Wunsch der Kunden Bauteile in hybrider Weise zu fertigen nachgegangen. Das folgende Beispiel zeigt einen Rohling für eine Vorkammerbuchse, wie diese in sehr vielen Spritzgießwerkzeugen eingesetzt wird, als Teil des Heißkanalsystems.
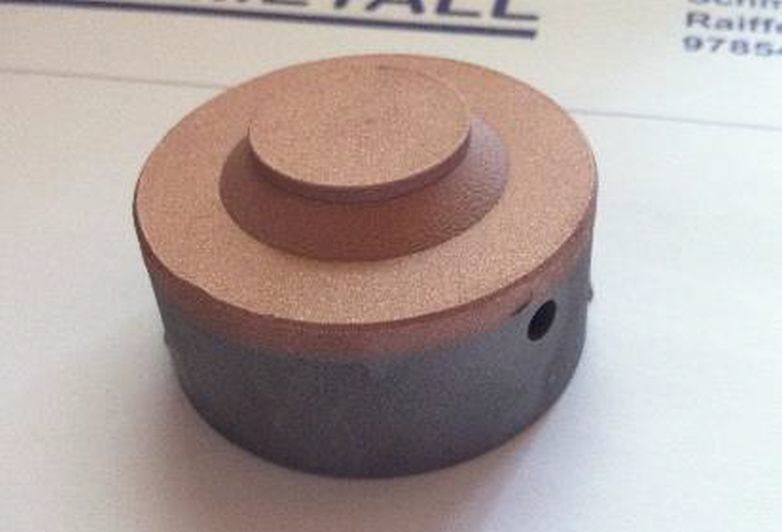 Bild 8: Rohling für eine Vorkammerbuchse in hybrider Bauweise
Dabei ist besonders zu beachten, dass der Unterbau konventionell aus einem Werkzeugstahl gefertigt wurde, bei dem die Wärmebehandlungsparameter denen der Hovadur®-Legierung entspricht.
Auch für eine weitere Legierung Hovadur® CCZ wurden die Prozess- und Wärme- behandlungsparameter entwickelt. Eine Legierung die meist aufgrund ihrer sehr hohen elektrischen Leitfähigkeit eingesetzt wird. Daher steht sie in vielen Anwendungsfeldern im Wettbewerb zu Reinkupfer. Ein besonderes Augenmerk lag auf der Entwicklung einer Wärmebehandlungsoption, die eine besonders hohe elektrische Leitfähigkeit ermöglicht.
Die folgenden Tabellen zeigen die Kennwerte gedruckter Bauteile aus der Legierung Hovadur® CCZ, analog zu der Vorgehensweise bei Hovadur® CNCS.
In Grün sind wieder die Kennwerte Härte und elektrische Leitfähigkeit an Zugproben gemessen neben denen an den Härte- und Leitwertproben ermittelten angegeben. In Rot die Datenblattwerte für geschmiedetes Halbzeug.
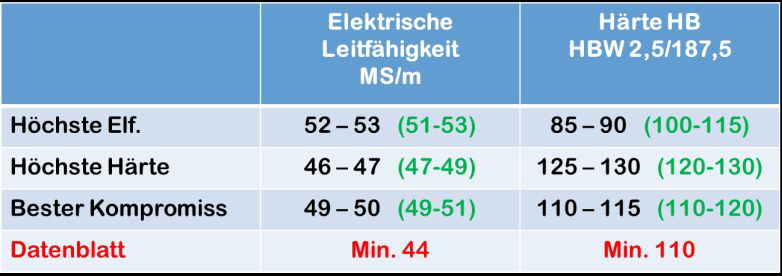 Bild 9: Kennwerte in Abhängigkeit der Wärmebehandlungsoptionen für Hovadur® CCZ
Besonders hervorzuheben ist hier die maximal erreichbare elektrische Leitfähigkeit, die mit 52-53 MS/m bei 90-92% von Reimkupfer liegt, bei jedoch deutlich höheren mechanischen Kennwerten.
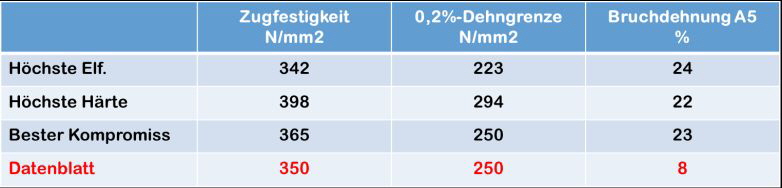
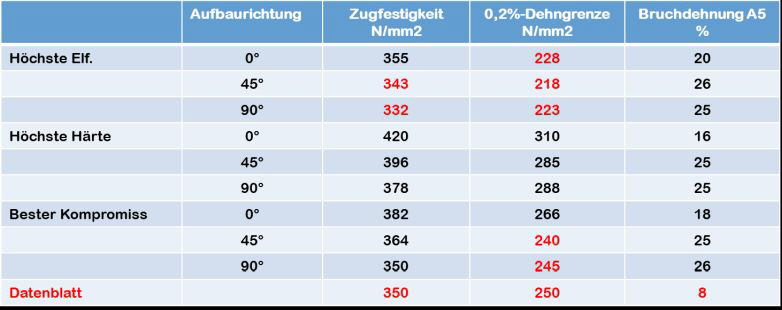 Bild 10: Mechanische Kennwerte gedruckter Bauteile aus Hovadur® CCZ
Diese Legierung wird zum Beispiel für Induktoren in Löt- oder Härteanlagen eingesetzt oder für Wärmetauscher.
In diesem Zusammenhang stellte sich immer wieder die Frage, wo liegt die kleinste realisierbare Wandstärke oder die filigransten Strukturen. Bei Induktoren haben wir mehrfach als kleinste Wandstärke 0,6 mm realisieren können, die kleinsten realisierbaren Strukturen konnten durch einen Postprozess Hirtisieren realisiert werden. Für einen Wärmetauscher wurden so Finnen in einer Dicke von ~150 µm gefertigt.
Eine besondere Herausforderung bei der Fertigung mittels PBF-LB Prozess stellen Beryllium-haltige Kupferlegierungen dar. Diese stellen insbesondere aufgrund der alveolengängigen Fraktion der Pulver ein erhebliches Risiko für die Mitarbeiter dar. In Verbindung mit den niedrigen Arbeitsplatz-Grenzwerten für Beryllium ist die eigentliche Herausforderung das Handling hochfeiner Pulver.
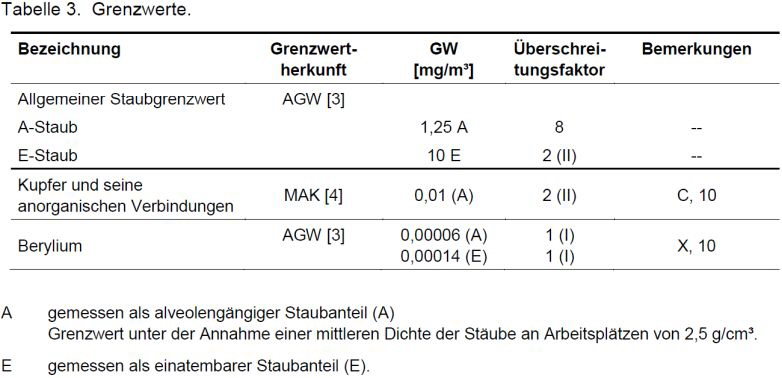 Bild 11. Zu berücksichtigende Arbeitsplatzgrenzwerte
Der herausragende Vorteil von Be-haltigen Kupferlegierungen liegt in der Kombination der Eigenschaften von hoher Leitfähigkeit und sehr guten mechanischen Kennwerten.
Erste Ergebnisse für die Hovadur®-Legierung CNBspez liegen bereits vor.
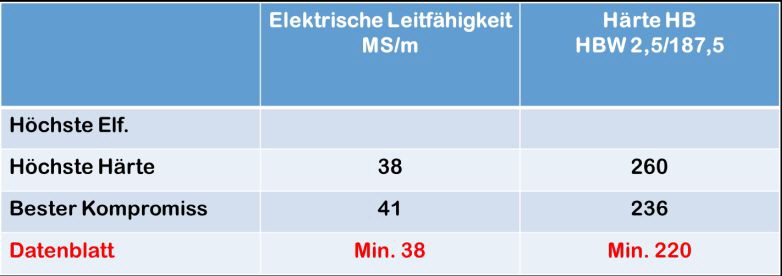 Bild 12: erste Kennwerte für gedruckte Bauteile aus Hovadur® CNBspez.
Die Ermittlung der Wärmebehandlungsoption für höchste elektrische Leitfähigkeit ist Gegenstand der laufenden Entwicklung ebenso wie die der mechanischen Kennwerte.
DED; Laserauftragschweißen Wir nutzen bei der Schmelzmetall das früher als Laserauftragschweißen, heute kurz DED Direct Energy Deposition, bezeichnete Verfahren um gezielt Komponenten aus einer Hovadur®-Legierung korrosions- und / oder verschleißgeschützt auszuführen. Über Kanale in einer Auftragsdüse werden mittels Schutzgasstrom verschleißfeste Werkstoffe wie Stellite oder Hartstoffe lokal auf einen Grundwerkstoff aufgetragen und mittels Laser der Grundwerkstoff und der Auftragswerkstoff aufgeschmolzen. Hierdurch wird eine metallurgische Anbindung des Auftragswerkstoffes an den Grundwerkstoff erreicht.
Exemplarisch stehen die folgenden Beispiele für die Möglichkeiten dieses Verfahrens in Verbindung mit Hovadur®-Kupferlegierungen.
Die Qualität und Standzeit von Spritzgießwerkzeugen ist entscheidend für die Produktqualität des Spritzteils und die Wirtschaftlichkeit. In Verbindung mit der konturnahen Kühlung von Formkernen wurde dies schon thematisiert. Zu den höchstbelasteten Komponenten eines Spritzgießwerkzeuges gehören die Komponenten im Heißkanal, wie Heißkanaldüse und Vorkammerbuchse, die mit bis zu 2.000 bar Innendruck belastet werden. Das Heißkanalsystem ist ein hochkomplexes Modul des Spritzgießwerkzeuges mit komplizierter thermischer Beanspruchung und punktuell hohen mechanischen und korrosiven Belastungen durch die Spritzmasse (Bild 13). Insbesondere bei korrosiven Kunststoffen, oder mit Glasfaser oder anderen Füllstoffen wie mit Flammschutzmittel gefüllten Thermoplasten.
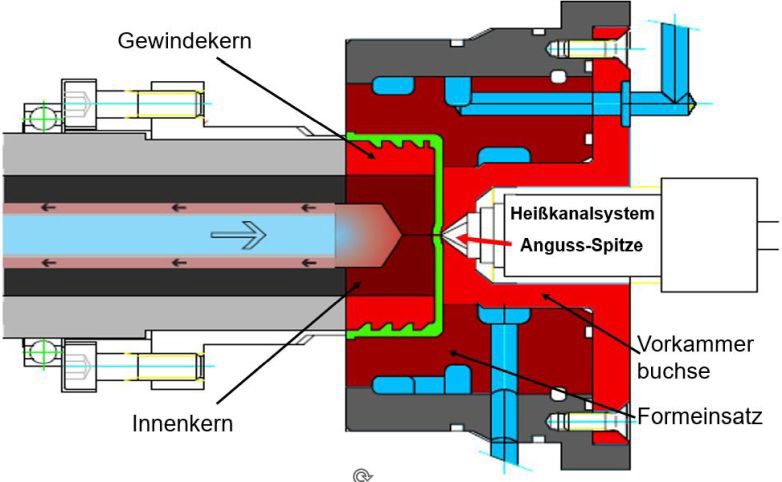 Bild 13: schematische Darstellung eines Spritzgießwerkzeuges -Kappenwerkzeug
Die folgenden Bilder zeigen verschiedene Angussdüsen, Angussspitzen bzw. Rohlinge für lokal verschleiß- geschützt ausgeführte Bauteile in Heißkanalsystemen.
 Bild 14: verschleißgeschützt ausgeführte Heißkanaldüsen
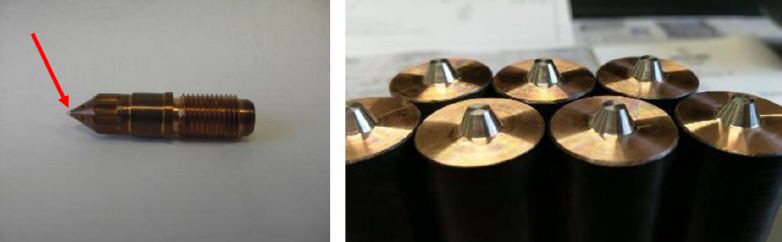 Bild 15: verschleißgeschützt ausgeführte Angussspitze und Rohling hierfür
Laserdispergieren Beim Leichtmetall-Druckgießverfahren wird flüssiges Metall unter hohem Druck und mit großer Geschwindigkeit (über 100 m/s) in Dauerformen aus Warmarbeitsstahl gegossen und erstarrt in diesen. Bei dem hier adressierten Kaltkammerverfahren wird das schmelzflüssige Metall in einem separaten Ofen bereitgehalten und über eine Dosiereinrichtung in die „kalte“ Gießkammer der Druckgussmaschine gebracht. Der Druckguss-Kolben bewegt sich in der Gießkammer und fördert die Schmelze zyklisch mit teils hoher Geschwindigkeit (in der zweiten Phase des Gießzyklus bis 7 m/s) in die Gussform. Zudem hat der Druckguss-Kolben die Aufgabe die Wärme aus Pressrest und Anschnitt abzuleiten, und so die Zykluszeit positiv zu beeinflussen. Die Standzeit des Kolbens hängt in erster Linie vom Kolbendurchmesser, der Kolbenkühlung- und Schmierung sowie den thermischen Verhältnissen in der Gießkammer und dem thermischen Impact in den Druckguss-Kolben ab. Bedingt durch sein Eigengewicht hängt der Kolben in Abhängigkeit der Kolbengröße durch, was zu Berührungspunkten mit der Gießkammer führt. Als Folge des Schleifkontaktes kommt es über die Prozesszeit zu Verschleißerscheinungen, eine ungleichmäßige Abnahme im Kolbendurchmesser ist die Folge. Vollkolben haben bedingt durch ihre einfache Bauweise den Vorteil eines einfachen Handlings und werden insbesondere von Gießereien eingesetzt, die ein großes Spektrum aktiver Formen im Einsatz haben, verbunden mit häufigem Formwechsel. Vollkolben aus Kupferlegierungen tragen durch die schnelle Wärmeabführung aus dem Gussteil und Anschnitt maßgeblich zu kürzeren Zykluszeiten bei. Um den Nachteil einer kürzeren Standzeit zu begegnen, soll durch eine hartpartikelverstärkte Lauffläche für Druckguss-Kolben aus Kupferlegierungen eine signifikant höhere Standzeit erreicht werden.
Dies wird erreicht, indem im Randbereich der Lauffläche mittels Laserdispergieren eine hartpartikelverstärkte Verbundwerkstoffschicht (metal matrix composite, MMC) erzeugt wird. Um den Laserdispergierprozess wirtschaftlich umsetzen zu können, ist die Erzielung hoher Flächenraten unabdingbar. Hierzu ist im Regelfall eine hohe Laserleistung erforderlich, unter anderem auch um Reflexionsverluste der Laserstrahlung am Kupferwerkstoff zu kompensieren. Eine Erhöhung der Laserleistung zum Ausgleich dieser Verluste sowie zur Bildung eines selbst bei hohen Vorschubgeschwindigkeiten hinreichend großen und tiefen Schmelzbades kann dazu führen, dass die Hartpartikel durch die Interaktion mit dem Laserstrahl beschädigt oder gänzlich zersetzt werden. Es muss daher eine geeignete Laserleistungsdichte in Abhängigkeit des Hartpartikelgehaltes gefunden werden, um einerseits eine ausreichende Schmelzbadbildung zu erzielen und andererseits eine Beschädigung der Hartpartikel zu vermeiden.
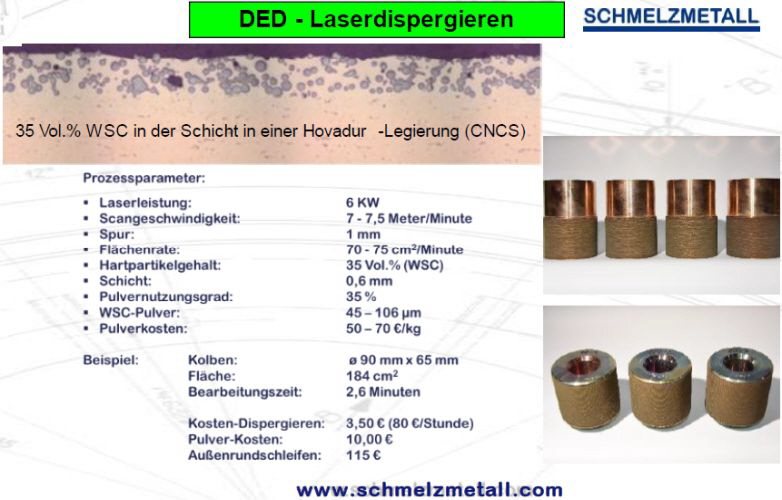 Bild 16. Erreichter Volumenanteil in der Randschicht, Prozessparameter und Kosten
Wie in Bild 16 zu sehen konnte eine 35Vol.% WSC (Wolframschmelzkarbid) – Schicht im Randbereich eines Kolbens aus Hovadur® CNCS erzeugt werden. Da der Markt für Druckguss-Kolben sehr preissensitiv ist konnte der Prozess Laserdispergieren durchaus wirtschaftlich dargestellt werden, jedoch bedingt die notwendige Bearbeitung des sehr eng tolerierten Außendurchmesser der Kolben ein Außenrundschleifen mit Diamantscheiben, was die Umsetzung im Markt deutlich erschwert.
Firmenprofil Seit 1959 ist die SCHMELZMETALL-Gruppe führender Hersteller von kupferbasierten Hochleistungswerkstoffen.
Vertreten sind wir auf der ganzen Welt durch international agierende Verkaufsteams und Niederlassungen. Unsere HOVADUR® Werkstoffe stehen für höchste Qualität und ein faires Preis-Leistungs-Verhältnis.
Durch mehr als 50 Jahre Erfahrung in der Herstellung von Kupferlegierungen im Hochvakuum erreichen wir die hohe qualitative Gleichmäßigkeit unserer Werkstoffe. Wir beherrschen die Weiterverarbeitung zu Halbzeugen und Fertigteilen und wissen, wie sich unsere Werkstoffe optimal in Ihren Aufgabengebieten und Anwendungen einsetzen lassen.
Zusammen mit der Beherrschung der Weiterverarbeitung zu Halbzeugen und Fertigteilen sowie dem Wissen über Einsatz und Anwendung der Legierungen ergeben sich für unsere Kunden einzigartige Vorteile:
Hochleistungswerkstoffe mit präzise abgestimmten Eigenschaften, die den unterschiedlichsten individuellen Anforderungen gerecht werden.
|