Was moderne Ultraschallgeneratoren heute leisten müssen, um die Anforderungen an Industrie 4.0 und vollautomatische Fertigungsprozesse zu erfüllen.
Mit dem Top-Thema Industrie 4.0 kommen auf Produktionsunternehmen immense Herausforderungen zu. Neben Automatisierungslösungen und Kommunikationsaufgaben sind es in verstärktem Masse Wiederholgenauigkeit bei gleichzeitig grösster Flexibilität sowie Prozesssicherheit und -stabilität, die gefordert werden. Und das auch bei Losgrösse eins. Für die Fertigungsprozesse Kunststoffschweissen, Metallschweissen und Trennschweissen mit Ultraschalltechnologie werden dafür Generatoren benötigt, die maximale Prozessstabilität und grösstmögliche Flexibilität bei verschiedensten Applikationslösungen gewährleisten. Worauf es genau ankommt, soll dieser Artikel aufzeigen.
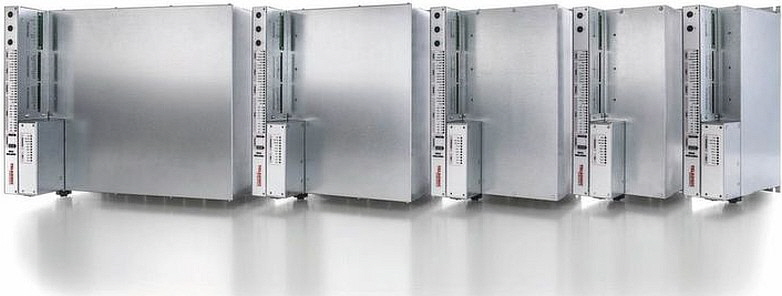 Die Multi-Applikations-Generatoren (MAG) bieten mit einem Leistungsbereich von 0,6 bis 7,2 kW ein breites Anwendungsspektrum bei großer Prozessstabilität
Wenn Produktionsmaschinen vollautomatisiert und miteinander verkettet sind und darüber hinaus untereinander kommunizieren, soll der Mensch im besten Fall gar nicht mehr eingreifen. Dazu müssen allerdings sämtliche Prozessschritte höchst stabil, prozesssicher und wiederholgenau ablaufen. Diese äusserst komplexen Anforderungen werden noch gesteigert, wenn es um kleine Serien mit häufigem Wechsel der Werkstücke, der Maschineneinstellungen und zahlreichen Rüstvorgängen geht. In der Königsdisziplin «vollautomatische Fertigung bei Losgrösse eins» wird dann alles auf die Spitze getrieben. Das gilt auch für die Fertigungsprozesse Kunststoffschweissen, Metallschweissen und Trennschweissen mit Ultraschalltechnologie.
Telsonic Ultraschalltechnologie bereit für Industrie 4.0 Die bewährte Ultraschalltechnologie eignet sich in zahlreichen Prozessen und Applikationen schon lange ideal für den automatisierten Einsatz. Sie bietet Lösungen sowohl für einfache als auch für anspruchsvolle Schweiss- und Trennaufgaben an Einzelarbeitsplätzen sowie in Produktionslinien und in Sonderanlagen. Typische Einsatzgebiete sind das Schweissen von Kunststoffen und Buntmetallen, das Trennschweissen von Vliesen, Portionieren von Lebensmitteln und viele weitere Anwendungen. In besonderem Fokus steht dabei vor allem die technologische Architektur des Ultraschallgenerators, der die Energie für die Schweissprozesse liefert. Industrie-Bussysteme schaffen die Grundlagen für die Datenkommunikation. Dabei ist Flexibilität gefordert da es in diesem Bereich diverse unterschiedliche Standards gibt. Erfolgreiche Ultraschall-Schweissungen benötigen ein Equipment und eine Kraft, die das oszillierende Werkzeug kontrolliert auf das Werkstück drückt. Das Ultraschall-Equipment besteht aus folgenden Komponenten:
• Ultraschall-Generator: erzeugt die elektrischen Hochfrequenz-Schwingungen • Konverter: wandelt die elektrischen Schwingungen in mechanische Schwingungen um • Booster: verstärkt (übersetzt) die mechanischen Schwingungen • Sonotrode: leitet die mechanischen Schwingungen ins Werkstück ein
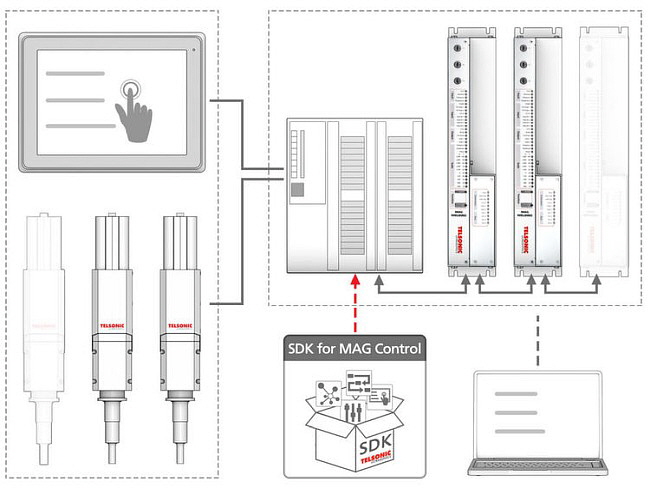 Das Telsonic SDK reduziert den Integrationsaufwand in SPS-gesteuerte Ultraschall-Schweissanlagen
Dem Generator kommen zentrale Aufgaben zu Die drei Komponenten Konverter, Booster und Sonotrode sind mechanisch fest miteinander gekoppelt und akustisch in Resonanz aufeinander abgestimmt. Um über ein solches Schwingsystem eine definierte Kraft auf das Werkstück einzuleiten, werden üblicherweise pneumatische Pressen und Vorschübe verwendet. Die Art und Weise der Vorschubsteuerung hat dabei einen wesentlichen Einfluss auf das Schweissresultat.
Erzeugt werden die Schwingungen im Generator, der die normale Netzspannung in Hochfrequenz umwandelt und diese Hochfrequenz an den Konverter überträgt. Damit kommt dem Generator eine Schlüsselfunktion zu. Durch die Digitalisierung der Industrie kommen für den Generator weitere Anforderungen hinzu. Aber was heisst das genau? Der Schweizer Pionier in der Ultraschalltechnologie, die Telsonic AG, hat jüngst eine Familie vollständig digitaler Multi-Applikations-Generatoren (MAG) vorgestellt. An deren Funktionalität und Leistungsspektrum lassen sich die aktuellen und zukünftigen Herausforderungen wunderbar aufzeigen.
MAG Generatorenfamilie erfüllt modernste Anforderungen Mit Schwingungsfrequenzen von 20-35kHz und Leistungsspitzen bis 7,2kW bieten sie ein breites Spektrum für viele Anwendungen. Das ist besonders interessant für Anlagenbauer und zur Integration in Sondermaschinen. Für die vollautomatisierte Produktion ganz wichtig, liegt diese Leistung unabhängig von Netzschwankungen über den gesamten Spannungsbereich konstant an. Auch Temperaturschwankungen lassen die MAG Generatoren kalt. Dafür sorgt die eingebaute Temperaturdriftkompensation von Telsonic. Die voll digitalisierten Generatoren verfügen über eine USB- und Industriebus-Schnittstellen. Schnell und einfach montierbare Busmodule gibt es für EtherNet/IP, ProfiNet, Sercos3, EtherCAT, Powerlink, Modbus und Profibus. So sind die Generatoren über diese modernen Bussysteme einfach zu konfigurieren und anzusteuern. In Echtzeit liegen die Ergebnisse der Schweissung wie Schweissdauer, Peak-Leistung sowie Schweiss- und Leistungskurven über die Zeit an der Steuerung vor. Durch die konfigurierbaren Ergebnisfenster ist eine umfangreiche Prozesskontrolle möglich. Das ist beispielsweise enorm wichtig für automatisierte Fertigungsprozesse in der Medizintechnik, wo eine Rückverfolgbarkeit bis zu zehn Jahre sichergestellt werden muss.
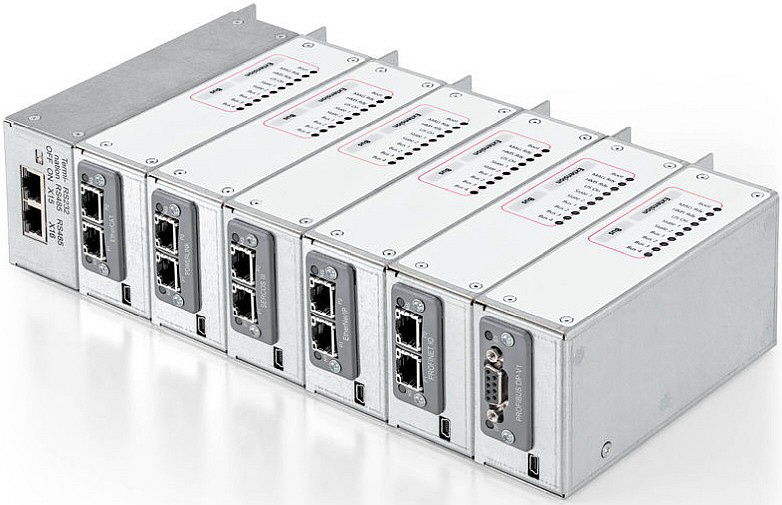 Die Generatoren lasssen sich über moderne Bussysteme einfach konfigurieren und anzusteuern
Vernetzbarkeit wichtig für Industrie 4.0 Wichtig für den Industrie 4.0 Gedanken und für Anlagenbauer ist die Vernetzbarkeit mit allen anderen Komponenten der Fertigung, die die Telsonic Generatorenfamilie MAG erfüllt. Als Multi-Applikations-Generatoren verfügen sie über Datensatz- und Frequenzumschaltung. Mit der Frequenzumschaltung lassen sich von ein und demselben Generator mehrere Schwingeinheiten sequenziell betreiben. Dabei können für bis zu 16 verschiedene Schwingeinheiten der Frequenz-Suchbereich, die Startfrequenz, Frequenzrampe und weitere Parameter gespeichert werden. Zusammen mit einer HF Umschaltung, die die übergeordnete SPS steuert, können so für jede Schwingeinheit die konfigurierten Frequenzparameter verwendet werden.
Mit der Datensatzumschaltung können Schweissparameter und die dazugehörigen Qualitätsfenster von extern über die Steuerleitungen oder den Feldbus ausgewählt werden. So wird beim Umbau auf eine andere Applikation oder beim Austausch des Amboss-Systems der entsprechende Schweissdatensatz geladen. Auch wenn eine Anlage mit dem gleichen Werkzeug mehrere Schweisspunkte an unterschiedlichen Stellen anfährt, und die einzelnen Schweissungen unterschiedliche Schweissparameter und Qualitätsfenster erfordern, wählt die übergeordnete Steuerung immer den richtigen Datensatz aus.
Praxisnahe Funktionen erleichtern Einsatz Gefordert wird auch, dass Generatoren extrem schnelle Anfahrtrampen erlauben. Das sorgt für maximale Produktivität in hochtaktenden Produktionslinien. Für kurze Rüstzeiten ist es von Vorteil, wenn kein Frequenzscan beim Sonotrodenwechsel notwendig ist, sondern die Generatoren sofort einsatzbereit sind. Bei den MAG-Generatoren von Telsonic lässt sich der Betriebszustand über ein gut ablesbares LED Status-Display auch aus der Entfernung erkennen. Inbetriebnahmen und Wartungsanalysen lassen sich mithilfe der Telsonic Software MAG Control Center bequem durchführen.
Dass die Generatoren in einer Platz sparenden Ausführung nur 265mm tief sind, prädestiniert sie für den Modul-zu-Modul Einbau in Schaltschränken mit nur 300mm Tiefe. Gegen zu grosse Wärmeentwicklung sorgt einerseits eine integrierte Aktivkühlung. Andererseits erzeugt auch schon die geringe Leistungsaufnahme der energieffizienten Generatoren grundsätzlich wenig Wärme. Das ermöglicht geringe Lüftungsabstände beim Modul-zu-Modul Einbau im Schaltschrank. Darüber hinaus sorgt die Blindstromkompensation für eine minimale Netzbelastung. Dadurch können die Leitungsquerschnitte kleiner gehalten werden.
Qualitative Prozesssteuerung als Bindeglied Zur Steuerung der MAG-Generatoren bietet Telsonic die Maschinen- und Prozesssteuerung TCS5 an. Anwender profitieren dabei von einer anwendungsfertig programmierten Schweisssteuerung mit intuitiver Bedienoberfläche, Peripheriesteuerung, Datenexport, Rechteverwaltung und weiteren Funktionen. Telsonic MAG Ultraschallgeneratoren liefern Effizienzsteigerungen und Stückkostenreduktion bei grosser Produktionssicherheit. Die für Industrie 4.0 Projekte benötigte Datenverfügbarkeit wird mit modularen Bus-Schnittstellen gewährleistet, welche auch hohe Flexibilität bei der Integration in übergeordnete Steuerungen bieten. So sind diese Ultraschall-Generatoren bereits heute in zahlreichen automatisierten Produktionsanlagen in der Automobil- und Verpackungsmittelindustrie erfolgreich im Einsatz.
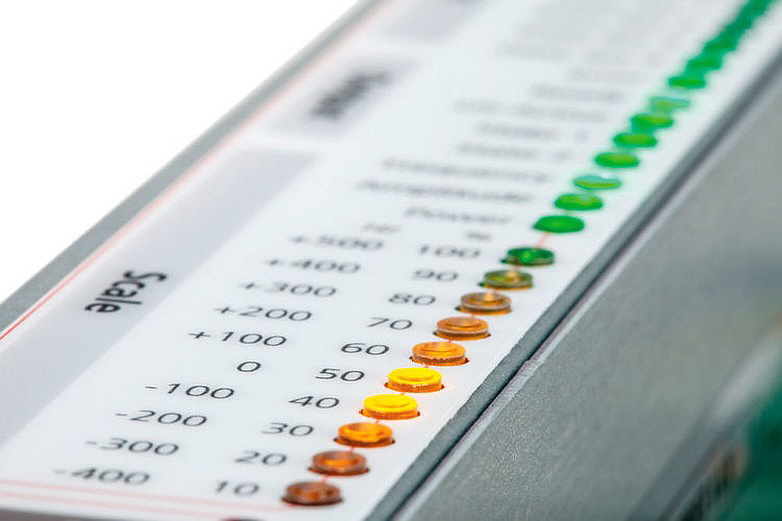 Bei den MAG-Generatoren von Telsonic lässt sich der Betriebszustand über ein gut ablesbares LED Status-Display auch aus der Entfernung erkennen
Innovative Ultraschalltechnologie aus der Schweiz Die Schweizer Telsonic Gruppe ist seit 1966 mit industriellen Ultraschall-Lösungen in Europa, Amerika und Asien vertreten. Ständige Innovationen tragen dazu bei, dass sich Telsonic in vielen Anwendungen einen Vorsprung erarbeitet hat der Kunden Mehrwert bietet. Mit über 250 hochqualifizierten Mitarbeitern ist das inhabergeführte Unternehmen auf das Kunststoff- und Metallschweissen, sowie das Reinigen und Sieben mit Ultraschall spezialisiert. Weltweit schätzen Kunden, unter anderem in den Branchen Automobil, Verpackung und der Medizintechnik, die umfassende Dienstleistungen und das breite Sortiment an Ultraschallkomponenten für den Anlagenbau sowie die kompletten Schweissanlagen.
• TELSONIC Imagebroschüre >>>
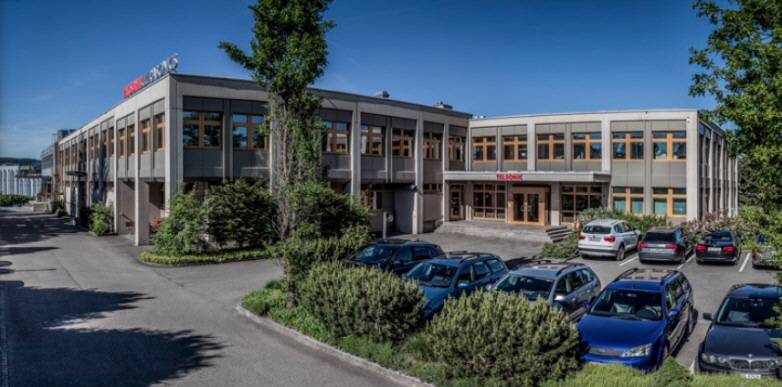
|