Deutscher Text >>>
A reliable process in the plastics injection molding Barnes Molding Solutions strategic business unit ‒ including brands FOBOHA, Gammaflux, männer, Priamus, Synventive and Thermoplay ‒ covers the entire spectrum of moldmaking and hot runner technology, including temperature control and process control technology. Molding Solutions’ strategy ensures that each brand of the company focuses on the development of its core competencies while close cooperation between the brands provides the customer with the best solution for the respective application.
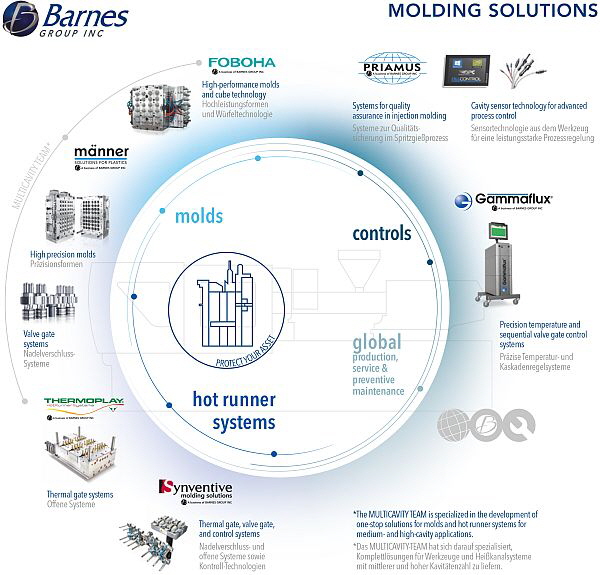 Barnes Molding Solutions is the world’s only supplier able to combine know-how in technology for injection molds, hot runners, monitoring and control systems
The expertise and know-how achieved during last years allow Molding Solutions to offer innovative solutions for demanding projects concerning the manufacture of plastic parts in the medical/pharmaceutical, personal care, packaging, automotive and technical parts markets, as well as electrical and household applications.
FOBOHA and männer, Barnes Molding Solutions’ high-precision moldmakers, serve different industries but work according to the same principles in terms of performance, durability, and ease of maintenance of their tools. While männer specializes in molds for the medical and pharmaceutical industries with corresponding knowledge in qualification, FOBOHA develops innovative mold concepts for the personal care and caps & closures end markets.
In hot runner technology, männer continues to focus on its “Cylindrical Valve Gate” patented by company founder Otto Männer, while Thermoplay specializes in thermal system designs. The two hot runner specialists complement each other to meet specific customer requirements.
Product news
New version of the 3 zones temperature controller TH-M6, compact and low-cost Thermoplay S.p.A. enriches its range of TH-M6 temperature controllers by offering a new 3 zones model, ideal for hot runners moulding applications with 1 and 2 points or single-nozzle injection systems.
Thermoplay is a business within Barnes Group Inc.’s Molding Solutions strategic business unit.
The new 3 zones temperature controller is a compact and low-cost product which presents the same characteristics as the 6 and 12 zones models.
A wide graphic display of 240x64 pixels allows the simultaneous visualisation of all information relevant to each single controlled zone and visualises the scrolling messages that can help the operator in case of alarm. The temperature controller continuously regulates the absorption of each zone and allows a prompt intervention in case plastic material leaks from an injector.
The temperature controller identifies and signals thermocouple failures (breakage and inverted connection), fuse and heater interruption, solid state relay faults, and interruption of one of the supply phases. On the front panel, 6 LED indicators are present for each zone, which signal any kind of malfunction of the control loop in a univocal way.
In case the thermocouple fails, the operator can submit a zone to another with the same thermal behaviour (“slave” function). This is a valid alternative to the manual operation.
The synchronous increase of temperatures function avoids heating differences in the various zones, due to the different characteristics of each heater during the machine start-up. Therefore, it is not necessary to resort to a delayed start-up of the zones relevant to nozzles anymore.
All regulation parameters and those referring to alarms can be collectively modified in all zones. The function is turned on through a button on the panel.
THM6 temperature controllers are available in 3, 6, and 12 zones configurations. The models 24-48 and EVO are also provided with a high performing operator terminal and offer additional features for monitoring and support through a local or remote network (Wi-fi or Ethernet).
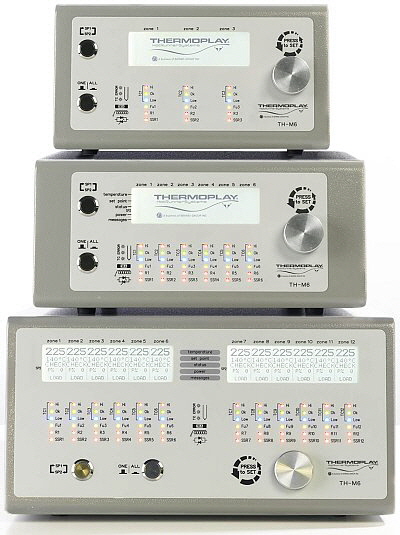 TH-M6 temperature controllers with 3, 6 and 12 zones
Integrated design and manufacture of injection systems “Webcreator” The online configurator “Webcreator” allows automatic configuration and manufacturing process of Thermoplay injection systems and generates the 2D and 3D CAD models, reducing the design and production time.
The design parameters can be inserted by web interface and the software generates the configuration and final assembly CAD drawings in the file format chosen by the user. The files are sent automatically to the user in real time.
The standard injection systems with 1,2,4,6, 8 and 16 injection points with or without shut off groups, and the related accessories have been transformed in a highly customizable product to follow the project settings.
The manifold can be configured in relation to the distance between nozzle axes, the injected material and the transformation temperatures. Flow channels size according to the type and diameter of the nozzle chosen.
Nozzles, injection bushing and accessories can be chosen throughout the standard range Thermoplay. The Webcreator allows to extend the standard product range and to reduce the production time, the costs and delivery time of injection systems.
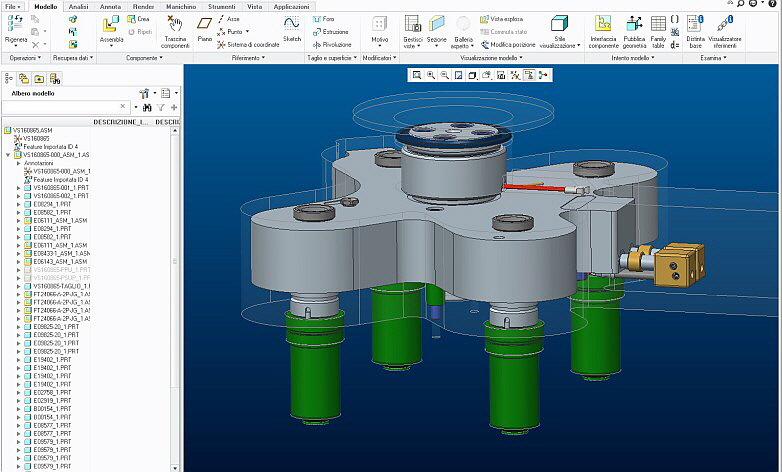
New Thermoplay nozzles “TF” and “TD” series for multicavity moulds Thermoplay presents its new range of hot runner systems for multicavity molds with up to 144 cavities.
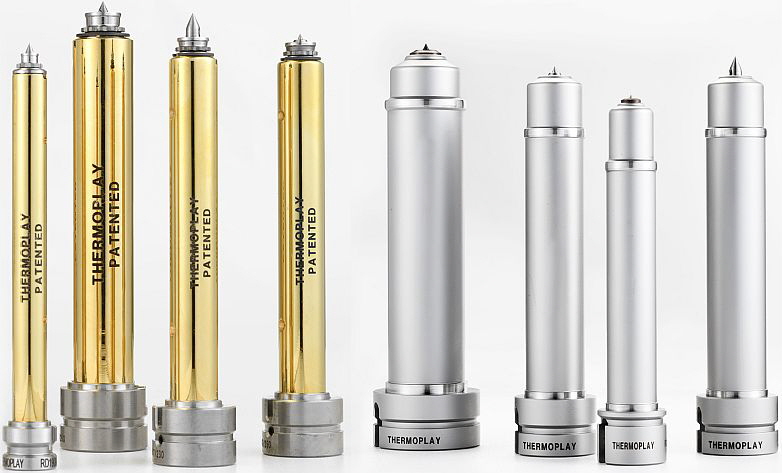 New Thermoplay nozzles “TF” and “TD” series for multicavity moulds
The new TF and TD nozzles offer significant process window improvements and an optimized thermal profile, which reduces energy consumption. This helps to ensure high reliability of the injection molding process and consistent part quality, even at the high speed and volumes specifically required for caps & closures, packaging, and personal care applications.
The new series are provided with a completely new tip that ensure optimal thermal conduction and the special steel construction allow to be used for the most polymers including technical resins. The heater and tip can be replaced directly in the injection molding machine.
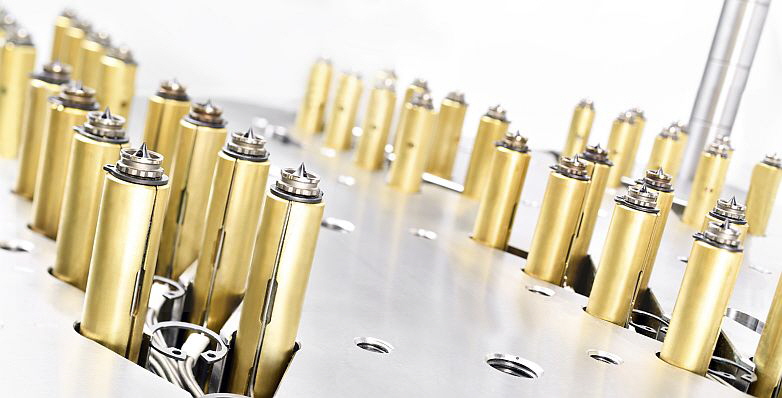 Thermoplay multicavity injection system
Männer, FOBOHA, and Thermoplay represent the multicavity team within the Barnes Molding Solutions strategic business unit, serving the market for medium- and high-cavity applications. The key strength of these three multicavity experts is several decades of experience with molds and hot runner technology as well as knowledge about their technical interaction. In addition, the hot runner division benefits from the extensive application knowledge of the moldmakers, which allows them to recommend the optimal hot runner design solutions to customers.
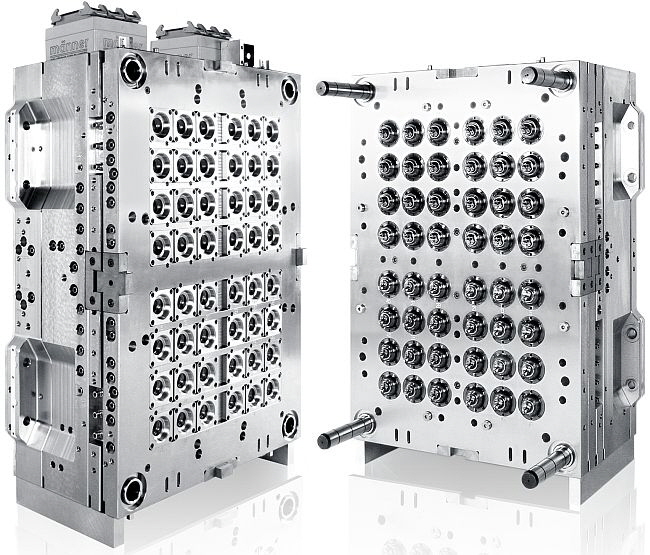 Männer 48 cavities mould with valve gate hot runner system
Within the area of control and regulation, Barnes Group has two companies with industry-leading expertise in its portfolio: Gammaflux is a specialist in the field of temperature control, and Priamus – the control technology pioneer – ensures optimum process control and state-of-the-art sensor elements.
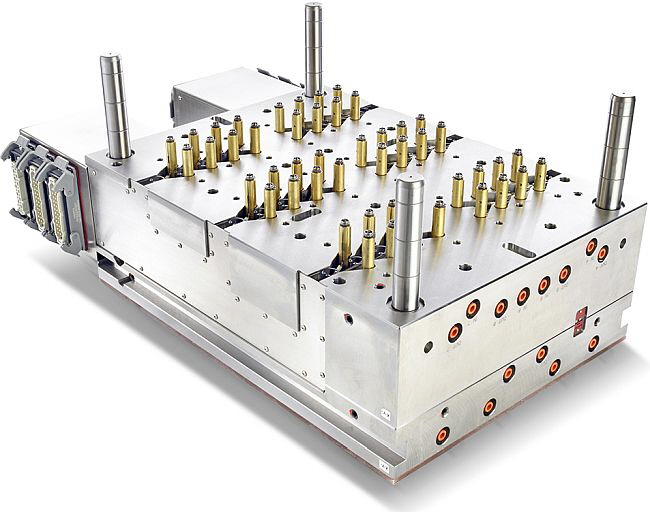 48 drops open gate Thermoplay hot half
A central topic is the process control of biopolymers and recycled materials, in which the inevitably higher process fluctuations are automatically regulated and compensated. These types of bio-plastics have long been recognized as important by Barnes Molding Solutions. In addition to customer projects that have already been completed, the strategic business unit continuously carry on research and developments projects in the extensive field of biologically produced, biodegradable, or even post-consumer recycled plastic (PCR).
Company profile
Thermoplay, with its HQ in the industrial area of Pont-Saint-Martin in Aosta, Italy, is a leading manufacturer of hot runner systems for the plastic injection moulding industry. As a result of continuous product development and considerable investment, Thermoplay is considered a global leader in hot runner system solutions.
Today, there are 190 employees in the manufacturing plant, which covers a surface of 11,000 square meters. Thermoplay is represented with sales and technical support teams in 48 countries. Thermoplay has also established sales and service branches in France, Germany, United Kingdom, Portugal, USA, Brazil, China and India.
Our product range, designed and built exclusively in-house, includes a vast selection of standard and special hot runner systems. Bi-colour and material mouldings can be produced through simultaneous injection of different colours and materials to satisfy all types of applications. Flow analysis is used to customize special hot runner solutions for family moulds and other demanding applications. Thermoplay manufactures an extensive range of temperature control units to fulfil the moulding process requirements.
Thermoplay SPA and its subsidiaries were acquired in August 2015 by Barnes Group Inc., a global industrial and aerospace manufacturer and service provider. Thermoplay joined Barnes Molding Solutions, a strategic business unit of Barnes Group, which provides high quality hot runners, molds and control systems to demanding global customers in the plastic injection molding industry.
Combined with Barnes Molding Solutions, Thermoplay’s technology, products, processes, and manufacturing capabilities provides an expanded suite of differentiated product offerings serving a broad range of customers in the plastic processing equipment marketplace.
The synergy of Barnes Molding Solutions’ businesses provides a broadened product offering, the highest level of global customer service and quality, and robust technologies for new and critical applications.
Visit us at the Swiss Plastics. We would be pleased to meet you on our booth: Hall 2 / Booth D 2113
|